Wire EDM Cutting Speed Calculator
FAQs
- What is the formula for cutting speed of wire EDM machine? The cutting speed formula for wire EDM is typically given as: Cutting Speed (mm/min) = Wire Feed Rate (mm/min) / Material Removal Rate (mm^2/min)
- What is the cutting tolerance of EDM wire? The cutting tolerance for wire EDM is generally in the range of 0.005 mm to 0.05 mm, depending on factors like machine precision and workpiece material.
- What are the parameters for cutting a wire EDM? Important parameters for wire EDM include wire tension, power settings, flushing rate, and workpiece material properties.
- How fast is a wire cutting machine? Wire EDM machines can have cutting speeds ranging from 20 mm^2/min to 300 mm^2/min, depending on the machine’s capabilities and the material being cut.
- What is the formula for cutting speed? Cutting Speed (mm/min) = Diameter of Workpiece (mm) x π x Rotational Speed (rpm)
- How do I calculate my cutting speed? To calculate cutting speed, you need to know the diameter of the workpiece and the rotational speed of the cutting tool (e.g., wire or electrode).
- What is the accuracy of wirecut EDM? The accuracy of wire EDM machines can be within ±0.005 mm to ±0.02 mm, but this can vary depending on machine quality and setup.
- How thick can a wire EDM cut? Wire EDM machines can cut materials as thick as 300 mm or more, depending on the machine’s power and the material’s properties.
- What is the standard wire tolerance? Standard wire EDM tolerance is typically around ±0.005 mm to ±0.02 mm, but it can vary based on specific requirements and machine capabilities.
- What is the spark gap in wire EDM? The spark gap in wire EDM is the distance between the wire electrode and the workpiece. It is usually maintained between 0.005 mm to 0.03 mm.
- What is KERF width in wire EDM? The KERF width in wire EDM is the width of material removed during the cutting process. It can range from 0.02 mm to 0.2 mm, depending on the machine settings and material.
- What is the maximum angle for wire EDM? Wire EDM can cut at angles up to 30 degrees or more, but the angle may affect cutting speed and accuracy.
- What is the speed of wire EDM wire? Wire EDM wire typically travels at speeds ranging from 1 m/s to 12 m/s.
- How do you cut wire faster? To cut wire faster in EDM, you can increase the power settings, optimize machine parameters, and use specialized high-speed wire.
- How long do wires take to execute? The time required for wire EDM operations depends on factors such as material thickness, complexity of the workpiece, and desired precision, but it can vary from minutes to several hours.
- What is rpm in cutting speed? RPM (Revolutions Per Minute) in cutting speed refers to the rotational speed of the cutting tool, such as the wire or electrode.
- What is the formula for machine cutting time? Machine Cutting Time (minutes) = Total Job Length (mm) / Cutting Speed (mm/min)
- How do you calculate cutting speed and feed? Cutting Speed (mm/min) = (Cutting Feed Rate (mm/tooth) x Number of Teeth) x Spindle Speed (rpm)
- How do you calculate cutting speed for grinding? The formula for calculating grinding cutting speed is: Cutting Speed (m/s) = (π x Grinding Wheel Diameter (mm) x Spindle Speed (rpm)) / 1000
- Can wire EDM cut at an angle? Yes, wire EDM can cut at various angles, including tapered cuts, by controlling the machine’s axis movements.
- What is the best wire for EDM? Brass wire is commonly used for EDM, but the choice of wire material can vary depending on the workpiece material and specific requirements.
- What is the white layer in wire EDM? The white layer, also known as the recast layer, is a layer of altered material on the workpiece surface that forms during EDM due to the heat generated. Its thickness can vary but is typically small, in the range of micrometers.
- What is the formula for wire cut calculation? There is no specific “formula” for wire cut calculation; it depends on the specific parameters and requirements of the wire EDM job.
- What are the disadvantages of wirecut EDM? Some disadvantages of wire EDM include slow cutting speeds for thick materials, high operating costs, and the need for skilled operators. Additionally, it may not be suitable for all materials.
- Can EDM cut diamond? EDM cannot cut diamond because diamond is an extremely hard and thermally conductive material that is resistant to EDM processes.
- What is the maximum current for wire size? The maximum current for wire EDM depends on the wire diameter and the machine’s capabilities. It can range from 1 ampere to 30 amperes or more.
- What is minimum wire resistance? The minimum wire resistance for wire EDM is typically around 0.01 ohms per meter, but it can vary with different wire materials.
- What is the minimum size AWG allowed for a fixture wire? The minimum size allowed for a fixture wire is often determined by safety and electrical code regulations and can vary. Commonly, 18 AWG or 20 AWG wires are used for fixtures.
- What is overburn in EDM? Overburn in EDM refers to the unintentional material removal beyond the intended cutting path due to factors like spark energy fluctuations or electrode wear.
- What is the minimum hole size for wire EDM? The minimum hole size that can be achieved with wire EDM is typically around 0.1 mm to 0.2 mm, but it can vary depending on the machine and material.
- What is the minimum spark gap in EDM? The minimum spark gap in EDM is usually maintained between 0.005 mm to 0.03 mm to ensure efficient machining.
- How wide should a KERF be? The width of the KERF depends on the specific wire EDM settings and material, but it can range from 0.02 mm to 0.2 mm or more.
- What is the difference between wire cut EDM and EDM? Wire cut EDM uses a wire electrode to cut materials, while traditional EDM uses a solid electrode. Wire EDM is often used for precision cutting, whereas traditional EDM is used for shaping and removing material.
- What is the width of EDM notch? The width of an EDM notch can vary widely, depending on the machine settings and material. It can range from fractions of a millimeter to several millimeters.
- What is the purpose of flushing during wire cut EDM? Flushing during wire EDM serves to remove debris and conductive materials from the cutting area, ensuring a clean and efficient machining process.
- Why is aluminum difficult to cut EDM? Aluminum is difficult to cut with EDM because it has a high thermal conductivity, which makes it dissipate heat quickly. This can lead to slower material removal rates and less efficiency in the machining process. Additionally, aluminum oxide buildup can occur on the workpiece surface during EDM.
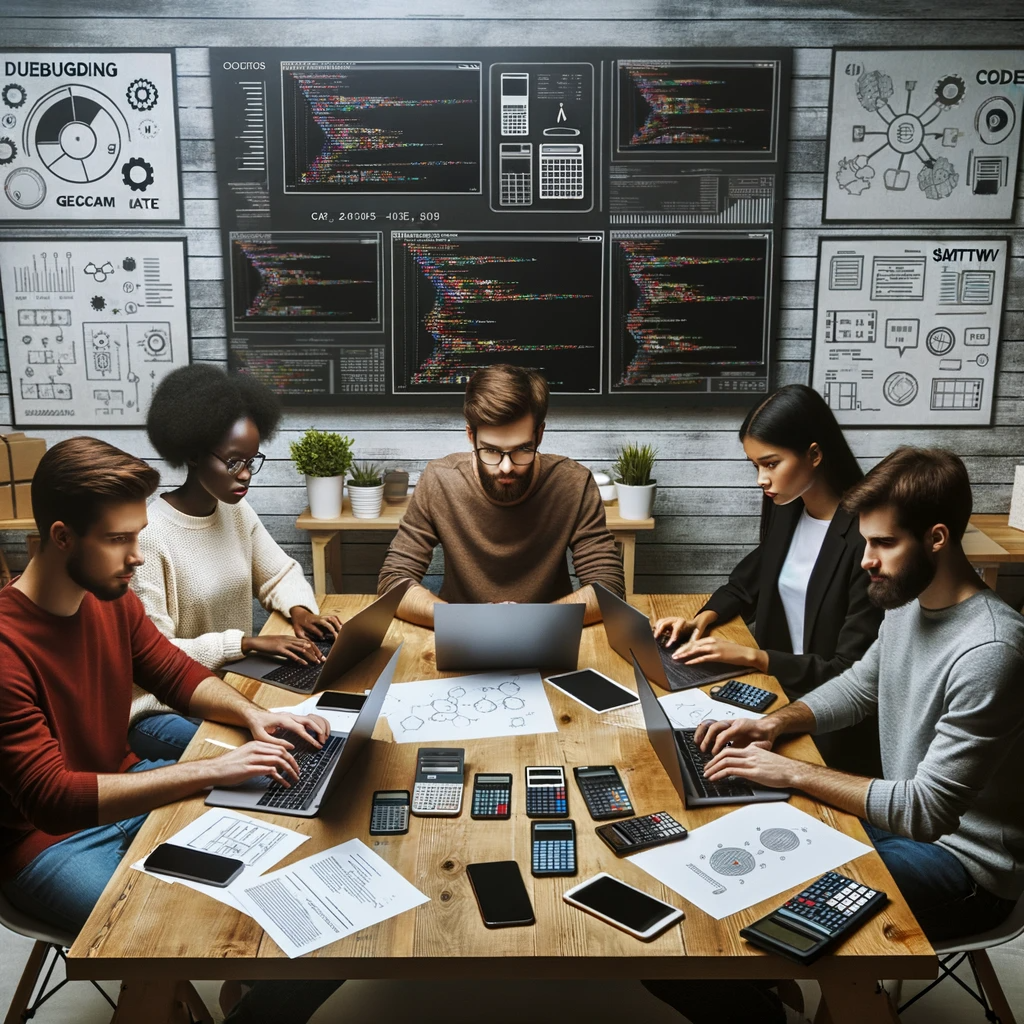
GEG Calculators is a comprehensive online platform that offers a wide range of calculators to cater to various needs. With over 300 calculators covering finance, health, science, mathematics, and more, GEG Calculators provides users with accurate and convenient tools for everyday calculations. The website’s user-friendly interface ensures easy navigation and accessibility, making it suitable for people from all walks of life. Whether it’s financial planning, health assessments, or educational purposes, GEG Calculators has a calculator to suit every requirement. With its reliable and up-to-date calculations, GEG Calculators has become a go-to resource for individuals, professionals, and students seeking quick and precise results for their calculations.