Warehouse space costs vary widely based on location, size, and amenities. On average, you can expect to pay anywhere from $4 to $10 per square foot per year. Prime urban locations tend to be more expensive, while rural areas offer more affordable rates. Additional services like temperature control and security can also increase costs.
Warehouse Space Cost Calculator
Region | Average Cost per Square Foot per Year |
---|---|
Rural Area | $4 – $6 |
Suburban Area | $6 – $8 |
Urban Area | $8 – $10 |
Prime Location | $10 – $15 |
Climate-Controlled (Additional) | $2 – $5 |
High-Security (Additional) | $1 – $3 |
FAQs
How do you calculate warehousing cost? Warehousing costs can vary widely depending on factors like location, size, and services provided. However, a basic way to calculate warehousing cost is to consider expenses such as rent or mortgage payments, utilities, insurance, equipment maintenance, labor, and any additional services (e.g., transportation, packaging) provided by the warehouse. Add up these costs on a monthly or annual basis to determine the total warehousing cost.
What is the average cost to run a warehouse? The average cost to run a warehouse can vary significantly depending on its size and location. However, as a rough estimate, warehouse operating costs can range from $4 to $7 per square foot annually. This cost includes expenses such as rent or mortgage, utilities, labor, insurance, maintenance, and other operational costs.
How do you calculate cost per unit in a warehouse? To calculate the cost per unit in a warehouse, divide the total warehouse expenses (including rent, labor, utilities, etc.) by the number of units stored in the warehouse during a specific period (e.g., monthly or annually). The formula is:
Cost per Unit = Total Warehouse Expenses / Number of Units
How many square feet is 2000 pallets? The number of square feet required for 2000 pallets depends on various factors such as the pallet size, stacking height, and aisle width. As a rough estimate, assuming standard pallet dimensions (48 inches by 40 inches) and single-deep racking, you might need around 40,000 to 50,000 square feet to store 2000 pallets.
What are generally warehouse costs? Warehouse costs typically include rent or mortgage payments, utilities (e.g., electricity, water), insurance, property taxes, equipment costs (e.g., forklifts, pallet racks), labor (wages and benefits for warehouse workers), security, maintenance, and any additional services like transportation, packaging, or handling.
How does warehouse pricing work? Warehouse pricing can vary depending on the provider and the services offered. Common pricing models include:
- Storage fees: Typically charged per square foot or pallet space.
- Handling fees: Charges for tasks like receiving, picking, packing, and shipping goods.
- Transportation fees: Costs associated with transporting goods to and from the warehouse.
- Value-added services: Extra charges for services like labeling, kitting, or quality control.
- Long-term vs. short-term rates: Discounts may apply for longer-term contracts.
How profitable is owning a warehouse? Warehouse profitability depends on various factors such as location, demand for storage space, operational efficiency, and management. While owning a warehouse can be profitable, it also comes with significant upfront costs and ongoing expenses. Profitability can vary widely, so it’s essential to conduct a thorough financial analysis before investing in a warehouse.
What percentage of warehouse cost is labor? Labor costs can vary significantly depending on factors like the level of automation and location. However, labor costs in a warehouse often account for 20% to 30% of the total operating expenses.
What is considered a large warehouse? The size of a large warehouse can vary by industry and location. Generally, a warehouse is considered large when it has more than 100,000 square feet of storage space. However, some industries, such as distribution and logistics, may consider warehouses with over 500,000 square feet as large.
What is the formula for cost price? The formula for cost price is:
Cost Price = Total Cost / Quantity
What is the formula to calculate cost? The formula to calculate cost is:
Total Cost = Fixed Costs + Variable Costs
What is labor cost per unit? Labor cost per unit is the cost of labor required to produce or handle one unit of a product or service. To calculate it, divide the total labor costs by the number of units produced or handled during a specific period.
What are 36×36 in pallets used for? Pallets measuring 36×36 inches are often used for smaller and lighter loads or in applications where space is limited. They are also commonly used in industries with specialized storage requirements, such as the pharmaceutical or food industries.
How full should a warehouse be? The ideal level of warehouse occupancy or “fill rate” depends on various factors, including inventory turnover, operational efficiency, and storage capacity. Generally, warehouses aim for an occupancy rate between 85% and 90% to allow for efficient movement of goods and accommodate fluctuations in inventory levels.
How many pallets can you fit in a 48 ft trailer? A standard 48-foot trailer can typically hold 26 to 30 standard-sized pallets, depending on factors like pallet size, load configuration, and trailer design.
What are overhead costs in a warehouse? Overhead costs in a warehouse include expenses that are not directly tied to the production or storage of goods. They can encompass rent or mortgage payments, utilities, insurance, administrative salaries, office supplies, and other indirect costs.
How big is an average warehouse? The size of an average warehouse can vary widely, but it is often between 25,000 and 200,000 square feet. Smaller warehouses can be even smaller, while larger distribution centers may span hundreds of thousands of square feet or more.
What is the biggest cost in a warehouse? The biggest cost in a warehouse can vary depending on the specific operation, but common significant expenses include labor, rent or mortgage payments, and transportation costs. Labor costs often make up a substantial portion of warehouse expenses.
What reduces warehousing cost? Several strategies can help reduce warehousing costs, including optimizing inventory levels, improving operational efficiency, implementing automation where possible, negotiating favorable lease terms, and regularly reviewing and adjusting your warehouse management processes.
What is a warehouse in and out fee? A warehouse in and out fee is a charge imposed by some warehouses for handling the movement of goods into and out of the facility. This fee covers tasks like loading and unloading trucks, inspecting incoming goods, and preparing shipments for outbound transport.
How can I save money in warehousing? To save money in warehousing, consider strategies like optimizing inventory levels, improving warehouse layout and organization, negotiating favorable contracts with suppliers and service providers, and investing in technology and automation to increase efficiency.
Who pays the most for warehouse workers? Wages for warehouse workers can vary by location, company, and job role. Generally, e-commerce and distribution companies in high-cost-of-living areas tend to pay higher wages to attract and retain skilled warehouse workers.
Are warehouses a good investment? Warehouses can be a good investment, especially in areas with strong demand for storage and distribution space. However, like any investment, they come with risks and require careful financial analysis and management.
What are the cons of buying a warehouse? Some potential cons of buying a warehouse include high upfront costs, ongoing maintenance expenses, property taxes, the need for significant capital investment, and the potential for market fluctuations affecting property value.
What is a good labor cost? A good labor cost depends on the industry, location, and job roles. In the warehousing industry, labor costs are often considered reasonable if they are in line with industry averages and do not significantly erode profitability.
What is a good labor rate? A good labor rate varies by location and job role. In the United States, for example, the federal minimum wage sets a baseline, but many states have higher minimum wage rates, and skilled or specialized labor may command higher hourly rates.
How do you quote labor costs? To quote labor costs, calculate the labor hours required for a specific job or project and multiply them by the hourly rate for the labor involved. Add any additional costs such as benefits or overtime if applicable.
What are the 5 types of warehouses? The five common types of warehouses are:
- Public Warehouses: Offer storage and distribution services to multiple clients.
- Private Warehouses: Owned and operated by a single company for its exclusive use.
- Distribution Centers: Focus on the efficient distribution of goods.
- Cold Storage Warehouses: Designed for storing perishable items at controlled temperatures.
- Automated Warehouses: Utilize robotics and automation for storage and retrieval.
What are the 5 areas of a warehouse? The five main areas of a warehouse are:
- Receiving Area: Where goods are received, inspected, and checked into inventory.
- Storage Area: Where products are stored in racks, bins, or shelving.
- Picking Area: Where workers gather items to fulfill orders.
- Packing Area: Where products are prepared for shipment, including packaging and labeling.
- Shipping Area: Where orders are loaded onto trucks for delivery.
What are the rules of warehouse? Warehouse rules typically include guidelines for safety, security, and efficient operations. These rules may cover aspects such as proper equipment use, handling hazardous materials, following inventory management procedures, and maintaining cleanliness and orderliness.
What are the 3 cost formulas? The three common cost formulas are:
- Fixed Costs: Costs that do not change with changes in production or sales volume.
- Variable Costs: Costs that vary in direct proportion to changes in production or sales.
- Total Costs: The sum of fixed and variable costs.
What is the formula for price per square foot? The formula for calculating price per square foot is:
Price per Square Foot = Total Price / Total Square Footage
What is CP formula? The CP (Cost Price) formula is:
CP = (Total Cost + Overhead Expenses) / Quantity
What is unit per labor hour? Unit per labor hour (UPLH) is a measure of productivity that indicates the number of units (e.g., products, tasks) produced or completed per hour of labor.
What is Labor Hour Rate? Labor Hour Rate refers to the cost of labor per hour for a specific job or task. It is calculated by dividing the total labor cost for that job by the number of labor hours required.
How do you calculate factory overhead? Factory overhead is calculated by adding up all indirect production costs, such as rent, utilities, maintenance, and depreciation, and then allocating these costs to each unit of production based on a predetermined allocation method.
What size pallets are worth money? Standard-sized pallets (e.g., 48 inches by 40 inches) are generally the most valuable because they are widely used and accepted in the industry. Specialty or custom-sized pallets may have less resale value.
Why are pallet prices so high? Pallet prices can vary based on factors such as supply and demand, lumber prices, and production costs. High demand for pallets during peak seasons or supply chain disruptions can drive prices up.
Who uses 48×40 pallets? 48×40 pallets are commonly used in various industries, including manufacturing, warehousing, retail, and logistics, for the storage and transportation of goods.
What is the best layout for a warehouse? The best warehouse layout depends on the specific needs of the operation. However, common layout designs include single-depth racks, double-depth racks, narrow-aisle racks, and flow-through racks, each tailored to optimize space and efficiency for different types of products and handling methods.
How do you maximize space in a warehouse? To maximize space in a warehouse, consider strategies such as efficient racking and shelving systems, vertical storage, mezzanine levels, optimized aisle widths, and regularly reviewing and reorganizing inventory.
What are the typical layouts at a warehouse? Typical warehouse layouts include:
- Single Aisle: A single central aisle with racks or shelving on both sides.
- Double Aisle: Two parallel aisles with racks or shelving in between.
- Cross-Docking: Direct movement of goods from receiving to shipping without storage.
- Bulk Storage: Large, open areas for storing bulk or oversized items.
- Flow-Through: Products enter at one end and exit at the other, suitable for high-throughput operations.
How many pallets fit in a 40ft truck? A standard 40-foot truck trailer can typically hold 24 to 30 standard-sized pallets, depending on factors like pallet size, load configuration, and trailer design.
Can you fit 30 pallets on a 53-foot trailer? Yes, a 53-foot trailer can often accommodate up to 30 standard-sized pallets, again depending on factors like pallet size and load configuration.
How far apart should pallets be? The distance between pallets in a warehouse depends on the type of storage and handling equipment used. Generally, pallets should be spaced to allow for safe and efficient movement, typically with enough space for forklifts or other equipment to access and maneuver between them.
What are the normal overhead costs? Normal overhead costs in a business can include rent or lease expenses, utilities (electricity, water, gas), insurance, office supplies, salaries of non-production staff, taxes, and depreciation of assets.
What are typical overhead costs? Typical overhead costs can include rent or mortgage payments, utilities, insurance, property taxes, administrative salaries, office supplies, and equipment maintenance.
How much should overhead expenses be? The ideal percentage of overhead expenses can vary by industry and business size. As a rough guideline, overhead expenses should ideally be kept below 20-30% of total revenue, but this can vary significantly.
What are the disadvantages of a small warehouse? Disadvantages of a small warehouse can include limited storage capacity, less efficient use of space, reduced ability to accommodate growing inventory, and potential limitations on handling larger or bulkier items.
How much space do I need for inventory? The amount of space needed for inventory depends on factors such as the type of products, volume, packaging, and storage method. Proper inventory management and organization are essential to determine the exact space requirements.
How big is a medium-sized warehouse? A medium-sized warehouse can vary, but it typically falls within the range of 25,000 to 100,000 square feet in terms of storage space.
Why is warehouse space so expensive? Warehouse space can be expensive due to factors such as location (high-demand areas have higher costs), rising property values, construction and maintenance costs, and the need for specialized infrastructure (e.g., climate-controlled facilities).
Which is the least expensive type of warehouse? Public warehouses, which offer shared storage and distribution services to multiple clients, are often the least expensive option because costs are distributed among multiple users.
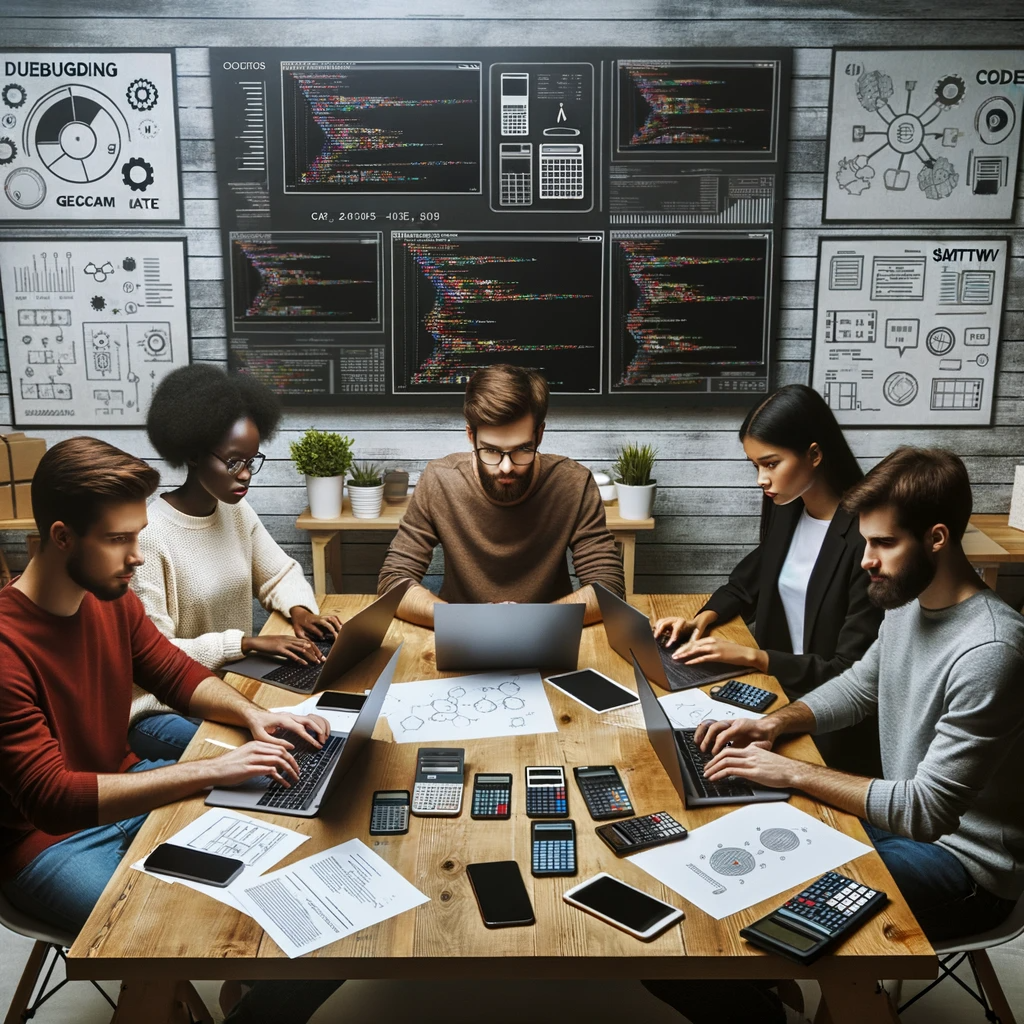
GEG Calculators is a comprehensive online platform that offers a wide range of calculators to cater to various needs. With over 300 calculators covering finance, health, science, mathematics, and more, GEG Calculators provides users with accurate and convenient tools for everyday calculations. The website’s user-friendly interface ensures easy navigation and accessibility, making it suitable for people from all walks of life. Whether it’s financial planning, health assessments, or educational purposes, GEG Calculators has a calculator to suit every requirement. With its reliable and up-to-date calculations, GEG Calculators has become a go-to resource for individuals, professionals, and students seeking quick and precise results for their calculations.