PCB trace width varies with current requirements. For a typical 1 oz copper PCB, approximate widths are: 10 mils (0.25 mm) for 1A, 40 mils (1.02 mm) for 2A, and 200 mils (5.08 mm) for 5A. Specific designs may require adjustments based on factors like temperature rise and copper weight. Always consult PCB design guidelines for accurate results.
PCB Trace Width vs. Current Calculator
Current (Amps) | Approximate Trace Width (mils) | Approximate Trace Width (mm) |
---|---|---|
0.1 | 4.0 | 0.10 |
0.5 | 20.0 | 0.51 |
1 | 40.0 | 1.02 |
2 | 80.0 | 2.03 |
5 | 200.0 | 5.08 |
10 | 400.0 | 10.16 |
20 | 800.0 | 20.32 |
50 | 2000.0 | 50.80 |
100 | 4000.0 | 101.60 |
FAQs
- How much current can a 10 mil trace carry? Estimation: A 10 mil (0.010 inches) trace on a typical 1 oz copper PCB can carry approximately 0.5-1 ampere of current.
- How do you calculate PCB trace width? PCB trace width can be calculated using online calculators or the IPC-2221 standard, which considers factors like current, temperature rise, and trace length.
- What is the width of a PCB trace for 2 amps? Estimation: For 2 amps of current on a 1 oz copper PCB, you might need a trace width of around 25-30 mils (0.025-0.030 inches).
- How much current can a PCB trace handle? The current-carrying capacity of a PCB trace depends on its width, thickness, temperature rise, and copper weight (e.g., 1 oz, 2 oz).
- What is the current of a 50 mil trace? Estimation: A 50 mil (0.050 inches) trace on a 1 oz copper PCB can typically handle around 5-7 amperes of current.
- What is the minimum trace width for current? The minimum trace width for current depends on the required current and the PCB’s copper weight. It could be as low as 5-10 mils for small currents.
- What is the rule of thumb for PCB trace width? Rule of Thumb: A common guideline is to use 10 mils (0.010 inches) trace width for every 1 ampere of current on a 1 oz copper PCB.
- What is the best trace width for PCB? The best trace width depends on your specific design requirements, including current, voltage, and thermal considerations. Consult PCB design guidelines or use calculators.
- What is common PCB trace width? Common PCB trace widths range from 4 mils (0.004 inches) for signal traces to 20-40 mils (0.020-0.040 inches) for power traces.
- What trace width for 100A PCB? Estimation: For a 100-ampere current on a 1 oz copper PCB, you might need a trace width of approximately 300-400 mils (0.300-0.400 inches).
- Can PCB traces be too wide? Yes, PCB traces can be too wide for low current applications, leading to inefficient use of PCB space and increased parasitic capacitance.
- How thick is 3 oz copper on a PCB? 3 oz copper on a PCB typically has a thickness of approximately 0.003 inches (3 mils or 0.0762 mm).
- What is the 3W rule for PCB trace? The “3W rule” suggests that the trace width should be three times the width of the component lead or pad that it connects to.
- How do you measure current in a PCB trace? You can measure current in a PCB trace using a current probe, a multimeter in current mode, or by using a shunt resistor to measure voltage drop across the trace.
- What is the max current for 0.254 mm trace? Estimation: A 0.254 mm (254 microns) trace on a typical 1 oz copper PCB can handle approximately 0.5-1 ampere of current.
- What is the trace width of 230V? Trace width is primarily determined by current, not voltage. The required trace width depends on the current flowing at 230V.
- How do you calculate how much current in amps is flowing? To calculate current, use Ohm’s Law: Current (I) = Voltage (V) / Resistance (R). Measure the voltage and resistance in the circuit.
- What is the tolerance for trace width? Tolerance for trace width depends on the specific PCB manufacturing process and design requirements. Common tolerances range from ±5% to ±10%.
- Does voltage matter for trace width? Voltage itself doesn’t directly affect trace width. Trace width is primarily determined by the current and thermal considerations.
- What is the trace spacing rule? Trace spacing depends on the desired level of isolation and can vary widely. Common values are 8 mils (0.008 inches) for general PCBs, but it can be smaller for high-density designs.
- How far should traces be from the edge of PCB? The distance between traces and the edge of a PCB depends on design requirements. It’s often recommended to keep traces at least 20-30 mils (0.020-0.030 inches) away from the edge.
- How thick is 1 oz copper? 1 oz copper on a PCB typically has a thickness of approximately 1.4 mils (0.0014 inches or 0.03556 mm).
- How thick is a normal PCB trace? A normal PCB trace can vary in thickness but is commonly around 1 oz copper (approximately 1.4 mils or 0.0014 inches).
- Are wider traces better? Wider traces are better for higher current applications but may not be suitable for low current or high-frequency signals due to increased parasitic capacitance.
- What is the rule of thumb for PCB trace inductance? The rule of thumb is that wider and shorter traces have lower inductance, which is desirable for high-frequency applications.
- How thick is PCB hard gold? PCB hard gold plating typically ranges from 30-50 microinches (0.00076-0.00127 mm) thick.
- How thick is high current PCB copper? High current PCBs may use copper thicknesses of 2 oz (approximately 2.8 mils or 0.07112 mm) or more for increased current-carrying capacity.
- When should I use 2 oz copper PCB? You should use a 2 oz copper PCB when you need to handle higher currents or require increased thermal performance.
- What is the 20h rule in PCB? The “20h rule” suggests that the height (H) of a trace above the ground plane should be at least 20 times its width (W) for controlled impedance traces.
- What are the rules for PCB traces? PCB trace rules encompass trace width, spacing, current-carrying capacity, and more. Specific rules depend on your design’s requirements and manufacturing process.
- Can you measure current without breaking the circuit? Yes, you can measure current without breaking the circuit using non-invasive methods such as current probes or current transformers.
- What is the current flow in a PCB? Current flow in a PCB depends on the specific design and circuit connections. It can range from microamperes to hundreds of amperes.
- How do you calculate the maximum current of a wire? The maximum current capacity of a wire is calculated based on its gauge (AWG) and temperature rating using reference tables or online calculators.
- How do you calculate the maximum current carrying capacity of a cable? The maximum current-carrying capacity of a cable is determined by factors like wire gauge, insulation, and temperature rating. Reference tables or manufacturer data can provide this information.
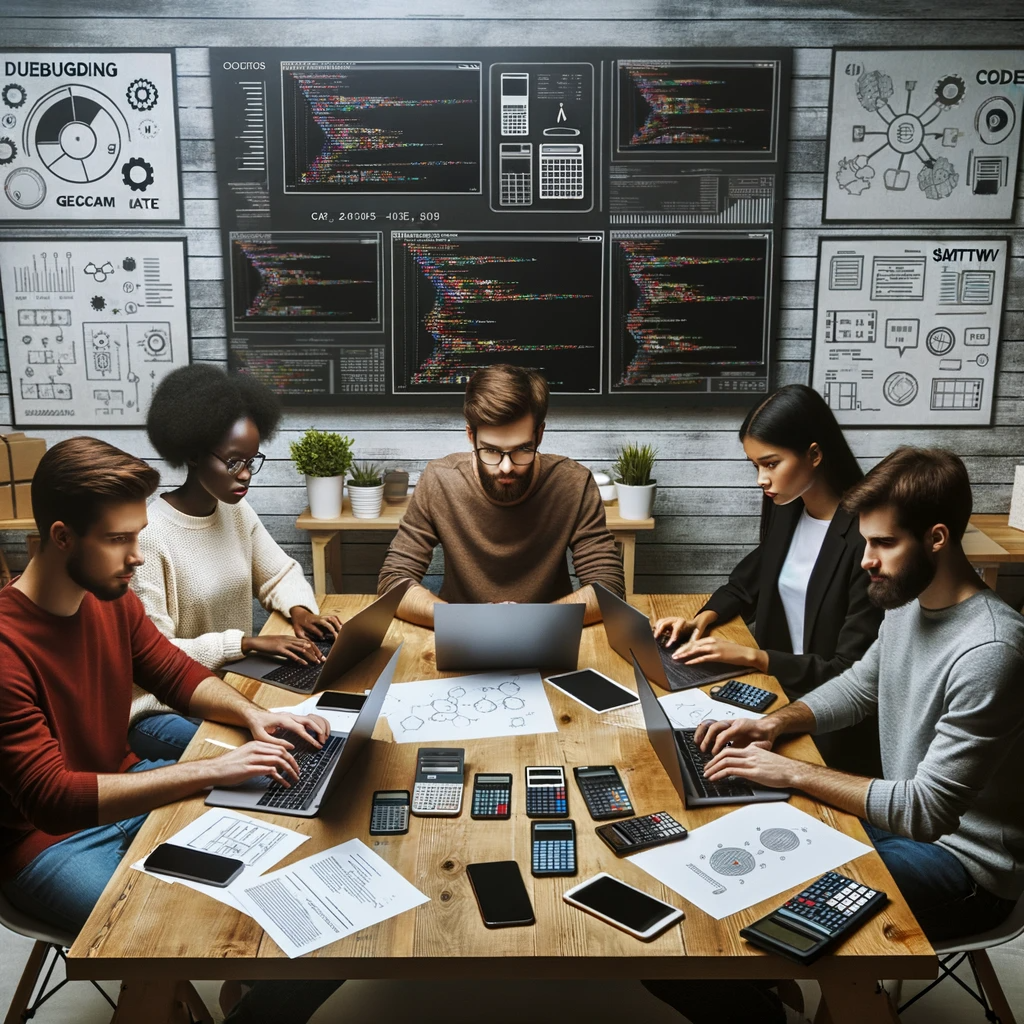
GEG Calculators is a comprehensive online platform that offers a wide range of calculators to cater to various needs. With over 300 calculators covering finance, health, science, mathematics, and more, GEG Calculators provides users with accurate and convenient tools for everyday calculations. The website’s user-friendly interface ensures easy navigation and accessibility, making it suitable for people from all walks of life. Whether it’s financial planning, health assessments, or educational purposes, GEG Calculators has a calculator to suit every requirement. With its reliable and up-to-date calculations, GEG Calculators has become a go-to resource for individuals, professionals, and students seeking quick and precise results for their calculations.