A tank strapping chart is a table that correlates liquid depth or level in a tank with the corresponding volume of liquid it contains. It is crucial for accurate inventory management, ensuring safety, and compliance with regulatory standards. Tank dimensions, such as diameter and length, are used to create these charts, allowing for precise volume calculations.
Tank Strapping Chart Calculator
Creating a complete tank strapping chart involves detailed measurements and calculations for a specific tank. I can provide a simplified example here, but please note that this example is for illustration purposes only and doesn’t represent an actual tank. Actual tank strapping charts are created based on precise measurements of the tank’s dimensions and may require specialized software or tools. Here’s a simplified example for a cylindrical tank:
Assumptions:
- Tank Type: Cylindrical
- Tank Diameter: 5 feet
- Tank Length: 10 feet
- Units: Gallons
Depth (Feet) | Depth (Inches) | Volume (Gallons) |
---|---|---|
0.00 | 0 | 0 |
1.00 | 12 | 73.63 |
2.00 | 24 | 294.51 |
3.00 | 36 | 664.17 |
4.00 | 48 | 1183.03 |
5.00 | 60 | 1851.85 |
6.00 | 72 | 2671.67 |
7.00 | 84 | 3663.89 |
8.00 | 96 | 4839.68 |
9.00 | 108 | 6200.33 |
10.00 | 120 | 7757.07 |
This simplified table shows the relationship between liquid depth in the tank (in feet and inches) and the corresponding volume of liquid in gallons. In practice, more precise measurements and calculations are necessary for accurate tank strapping charts, especially for non-cylindrical tanks or tanks with irregular shapes.
FAQs
How do you read a tank strapping chart?
A tank strapping chart, also known as a tank calibration chart, is used to determine the volume of liquid inside a tank based on its level or depth. To read the chart, you need to find the depth or level of the liquid in the tank on the chart’s horizontal axis and then read the corresponding volume measurement on the vertical axis.
How is tank strapping done?
Tank strapping, or tank calibration, is typically done by measuring the tank’s dimensions and then determining its volume at different liquid levels. This involves using a calibrated tape measure or laser device to measure the distance from the top of the tank to the liquid surface at various points. These measurements are then used to create a tank strapping chart.
How do you make a dip chart for a tank?
To make a dip chart for a tank, you measure the distance from the top of the tank to the liquid surface at multiple points and record these measurements along with the corresponding volumes of liquid in the tank. You then use this data to create a chart that shows the relationship between the liquid level and volume.
How many inches is a 275 gallon tank?
A standard 275-gallon tank typically measures about 44 inches in height, 27 inches in width, and 60 inches in length.
How do you check peaking and banding in a tank?
Checking peaking and banding in a tank involves measuring the thickness of the tank’s bottom plate and shell in various locations. Peaking refers to a localized upward deformation of the tank’s bottom, while banding is the circumferential deformation around the tank’s shell. Ultrasonic thickness gauges are commonly used for this purpose.
What is the strapping method of tank calibration?
The strapping method of tank calibration involves measuring the dimensions of the tank and creating a calibration chart (strapping chart) that relates liquid depth or level to the corresponding volume of liquid in the tank. This method is used to accurately determine the tank’s volume at different fill levels.
What is deadwood in tank calibration?
Deadwood in tank calibration refers to the space or volume inside a tank that cannot be used to store liquid due to obstructions, such as structural supports, pipes, or other internal components. It is essential to account for deadwood when creating a tank strapping chart for accurate volume calculations.
How are tanks gauged?
Tanks are gauged using various methods, including float gauges, radar level sensors, ultrasonic level sensors, and manual methods like dip sticks or tape measures. These instruments measure the level of liquid inside the tank, which can then be used to calculate the volume.
What is the primary purpose of a tank chart?
The primary purpose of a tank chart (strapping chart) is to provide a quick and accurate way to determine the volume of liquid inside a tank based on its level or depth. It is essential for inventory management, monitoring fluid levels, and ensuring the safe and efficient operation of tanks.
How do you design a tank size?
The design of a tank size depends on several factors, including the intended use, the volume of liquid to be stored, available space, regulatory requirements, and structural considerations. It typically involves calculations and engineering to ensure the tank meets specific criteria and standards.
What is the code for tank design?
Tank design codes can vary by region and purpose. Common tank design codes include API 650 for atmospheric storage tanks and API 620 for low-pressure storage tanks. ASME Boiler and Pressure Vessel Code may also apply to some tanks.
How much does a 275 gallon water tank weigh when full?
A 275-gallon water tank, when full, can weigh approximately 2,100 to 2,400 pounds, depending on the specific design and materials used.
How many gallons is a full 275 gallon tank?
A full 275-gallon tank contains 275 gallons of liquid.
How much does a 275 gallon gas tank weigh?
The weight of a 275-gallon gas tank can vary depending on the material it’s made of and whether it’s full or empty. When full, it can weigh around 2,000 to 2,300 pounds.
What is the difference between banding and peaking?
Banding refers to circumferential deformations around the shell of a tank, often caused by external pressure or uneven settlement. Peaking is a localized upward deformation of a tank’s bottom due to excessive internal pressure or overfilling.
How do you do a hydrostatic test on a tank?
A hydrostatic test on a tank involves filling the tank with water or another suitable liquid to a specified pressure level and holding it there for a defined period. The purpose is to check for leaks, structural integrity, and the ability of the tank to withstand pressure.
How do you measure peaking?
Peaking in a tank is typically measured using ultrasonic thickness gauges or other non-destructive testing methods. These instruments measure the thickness of the tank’s bottom plate and detect localized upward deformations.
How often should a tank be calibrated?
The frequency of tank calibration depends on factors such as regulatory requirements, the type of tank, the stored product, and its usage. Tanks may need calibration annually, every few years, or as specified by industry standards and regulations.
What is the tank bottom inspection technique?
Tank bottom inspection techniques involve examining the bottom of a tank for corrosion, pitting, leaks, and other defects. Common methods include visual inspection, magnetic particle testing, and ultrasonic testing.
How do you check the calibration of a tape measure?
To check the calibration of a tape measure, you can compare it to a known, accurate standard. Measure a length with the tape measure and then measure the same length with the standard. Any discrepancy indicates the need for calibration or adjustment.
How do you calibrate a rough balance?
Calibrating a rough balance involves adjusting its weights and ensuring they are accurate by comparing them to known standard weights. Adjustments are made until the balance readings match the expected values.
How do you calibrate a tank volume?
Calibrating tank volume involves creating a tank strapping chart that relates the tank’s dimensions (such as length, width, and depth) to the volume of liquid it contains at different levels. This calibration chart is used for volume calculations.
How do you calibrate a dry block?
Calibrating a dry block involves heating or cooling it to known temperature values and using calibrated temperature sensors to verify its accuracy. Adjustments are made if necessary to ensure the block maintains the correct temperature.
What does 90% ullage mean?
Ullage refers to the empty space or gap at the top of a container or tank that is not filled with liquid. 90% ullage means that the container is filled to 90% of its capacity, leaving 10% of the space empty.
Why are tanks filled from the bottom?
Tanks are often filled from the bottom to reduce the risk of entraining air or introducing contaminants into the stored liquid. Filling from the bottom helps maintain the integrity and quality of the liquid.
Why are tanks hand loaded?
Tanks may be hand-loaded for small-scale operations or when automation is not cost-effective. Hand loading allows for precise control over the filling process and is suitable for low-volume applications.
What is the gun of a tank called?
The main gun of a tank is commonly referred to as the “tank gun” or simply the “main gun.”
What is the top of a tank called?
The top of a tank is often called the “tank roof” or “tank lid.” It can vary in design and functionality depending on the type of tank.
Can a tank move without tracks?
Tanks typically rely on tracks for mobility, but some tank-like vehicles, such as wheeled armored vehicles, use wheels instead of tracks for movement. These vehicles are designed for specific operational requirements.
What is the ideal tank ratio?
The ideal tank ratio depends on the specific application and purpose of the tank. Factors to consider include volume, shape, material, and structural integrity, which can vary widely across different industries.
What is the ideal tank shape?
The ideal tank shape also depends on the intended use. Common tank shapes include cylindrical, rectangular, and spherical, with the choice influenced by factors like storage capacity, space constraints, and ease of manufacturing.
How big does my tank need to be?
The size of a tank needed depends on the purpose it serves, the volume of liquid to be stored, and any relevant regulations or standards. Detailed calculations and engineering considerations are typically required to determine the appropriate tank size.
How full should you fill a tank?
The level to which a tank should be filled depends on its design, safety considerations, and operational requirements. Tanks are typically not filled to 100% capacity to allow for expansion and prevent overflows.
What is the NFPA code for tanks?
The National Fire Protection Association (NFPA) has various codes related to tanks depending on their use. NFPA 30 deals with flammable and combustible liquids, including storage tanks.
What is the T code for tanks?
The “T code” for tanks typically refers to the United Nations (UN) packaging code, which is used to classify and identify tanks and containers for the transportation of hazardous materials.
How to design a tank farm?
Designing a tank farm involves determining the number, size, and layout of tanks based on factors such as the type of product stored, storage capacity requirements, safety regulations, and environmental considerations. It often requires engineering expertise and adherence to applicable codes and standards.
How long does a 275 gallon tank last?
The lifespan of a 275-gallon tank can vary depending on factors such as the material, maintenance, and environmental conditions. Properly maintained tanks can last for many years, but they may need periodic inspections and maintenance to ensure their longevity.
How heavy is a 250 gallon water tank?
The weight of a 250-gallon water tank can vary depending on its material and design. On average, a plastic 250-gallon tank may weigh around 100 to 150 pounds when empty.
How much does a 300 gallon tank weigh with water?
A 300-gallon tank, when filled with water, can weigh approximately 2,500 to 2,700 pounds, depending on the specific design and materials used.
How many gallons is 3/4 of a 275 gallon tank?
Three-quarters (3/4) of a 275-gallon tank is equivalent to 206.25 gallons.
How much heating oil can you put in a 275 gallon tank?
A 275-gallon tank can typically hold up to 275 gallons of heating oil when full.
How many gallons is 1/4 of a 275 gallon tank?
One-quarter (1/4) of a 275-gallon tank is equivalent to 68.75 gallons.
What are the dimensions of a 275 fuel tank?
A standard 275-gallon fuel tank typically measures about 44 inches in height, 27 inches in width, and 60 inches in length.
How heavy is a 275 gallon tote?
A 275-gallon tote, when empty, can weigh around 100 to 150 pounds, depending on the material used in its construction.
How many inches is a 275 gallon tank?
A standard 275-gallon tank typically measures about 44 inches in height, 27 inches in width, and 60 inches in length.
How does banding work?
Banding in the context of tank inspection refers to measuring the thickness of the tank shell at various circumferential locations to check for deformations or corrosion.
What is the difference between layers and banding?
In tank inspection, “layers” typically refer to the individual rings or sections of the tank’s shell, while “banding” refers to measuring the thickness of the tank’s shell at various circumferential positions to assess its condition.
What is a banding approach?
A banding approach in tank inspection involves systematically measuring the thickness of the tank’s shell in bands or sections to identify any abnormalities or variations in thickness.
How often should tanks be hydrostatically tested?
The frequency of hydrostatic testing for tanks depends on regulatory requirements, industry standards, and the type of tank. Common intervals can range from 1 to 10 years or more.
What are the rules for hydrostatic test?
The rules for a hydrostatic test include filling the tank with a liquid, pressurizing it to a specified level, monitoring for leaks or structural issues, and ensuring compliance with safety and testing standards.
What is the standard for hydrostatic test?
The standards for hydrostatic testing vary depending on the type of tank and its intended use. Common standards include API 650 and API 620 for storage tanks, which specify testing requirements.
How do you check banding of tanks?
To check the banding of tanks, you measure the thickness of the tank’s shell at various circumferential positions using ultrasonic thickness gauges or other non-destructive testing methods. This helps identify deformations or corrosion.
What is peaking in pipe?
Peaking in pipes is a phenomenon where the pipe’s diameter temporarily increases due to internal pressure or a temporary surge in fluid flow. It can cause stress on the pipe and should be monitored and managed.
How many times should your tank cycle per hour?
The number of times a tank cycles per hour depends on its purpose and the specific system it’s part of. For example, in heating or cooling systems, tanks may cycle multiple times per hour to maintain temperature control.
What is the calibration chart of a tank required for?
A calibration chart of a tank is required to accurately determine the volume of liquid inside the tank at different levels. It is essential for inventory management, process control, and ensuring compliance with regulatory standards.
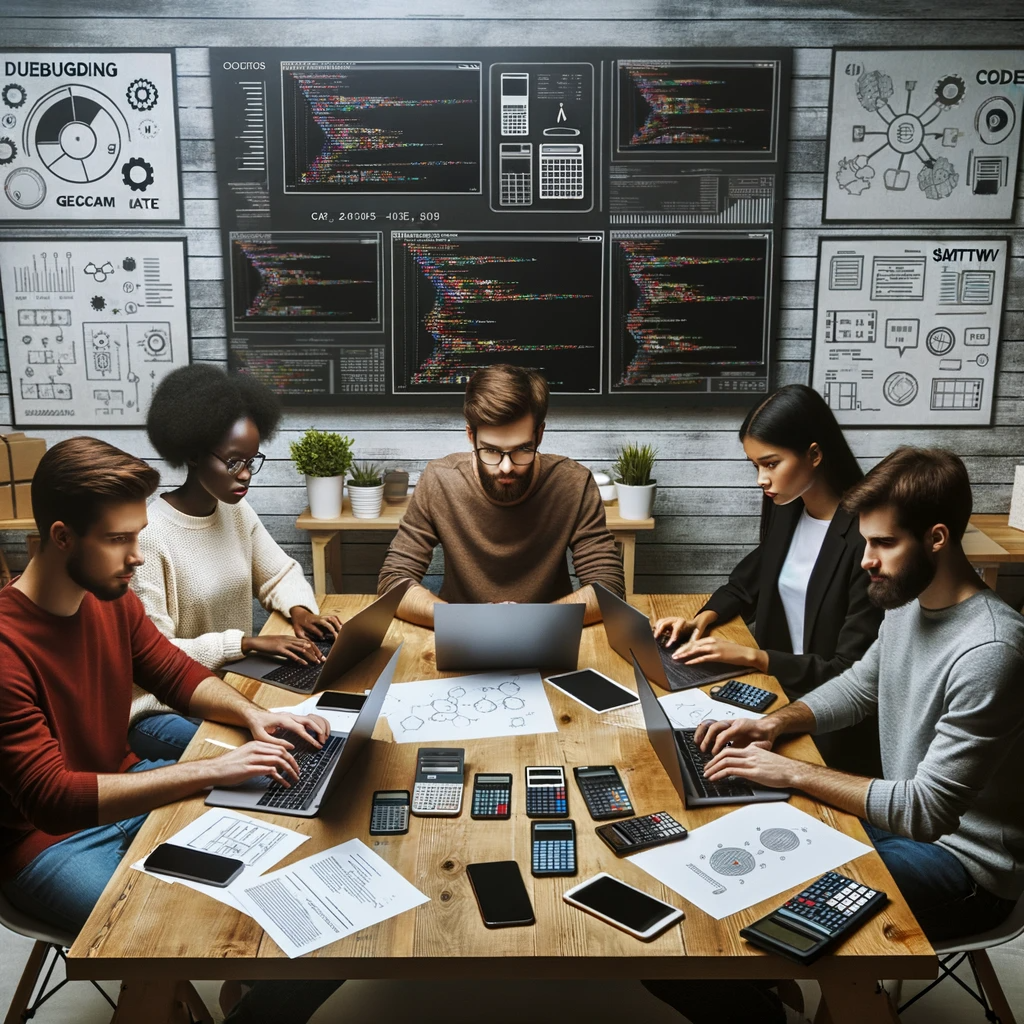
GEG Calculators is a comprehensive online platform that offers a wide range of calculators to cater to various needs. With over 300 calculators covering finance, health, science, mathematics, and more, GEG Calculators provides users with accurate and convenient tools for everyday calculations. The website’s user-friendly interface ensures easy navigation and accessibility, making it suitable for people from all walks of life. Whether it’s financial planning, health assessments, or educational purposes, GEG Calculators has a calculator to suit every requirement. With its reliable and up-to-date calculations, GEG Calculators has become a go-to resource for individuals, professionals, and students seeking quick and precise results for their calculations.