Surface roughness refers to small-scale irregularities on a surface. It’s measured using parameters like Ra (average roughness) and Rz (maximum height). Common units include micrometers (μm) and microinches (μin). It’s vital in industries like manufacturing to ensure product quality, affect friction, wear, and sealing properties. Specific applications may require different roughness levels for optimal performance.
Surface Roughness Calculator
Rz (Average Maximum Roughness):
Term/Parameter | Description |
---|---|
Surface Roughness | A measure of the small-scale irregularities or deviations from a smooth surface profile. |
RA (Arithmetical Mean Roughness) | The average of the absolute values of deviations from a mean line over a specified measurement length. |
Rz (Maximum Height of the Profile) | The maximum vertical distance between the highest peak and the deepest valley within a sampling length. |
Rt (Total Roughness) | The total height difference between the highest peak and the lowest valley over the entire surface. |
Surface Finish | The quality and appearance of a surface, often characterized by Ra values or specific finishes. |
Measurement Units | Surface roughness is typically measured in micrometers (μm) or microinches (μin). |
Common RA Values | – 0.2 μm to 1.6 μm: Good for many industrial applications. |
– < 0.2 μm: Very smooth surface. | |
– > 1.6 μm: Relatively rough surface. | |
Common Surface Finishes | – #4 Finish: Brushed or satin finish with Ra around 0.4 to 0.8 μm. |
– #8 Finish: High-polish finish with Ra below 0.2 μm. | |
Measurement Methods | – Profilometer: Directly measures surface roughness by tracing the surface profile. |
– Non-contact Optical Profilometry: Uses optical methods to measure surface roughness. | |
Importance of Surface Roughness | – Affects functionality, appearance, and performance of components. |
– Critical in sealing, friction, wear, and fatigue properties. |
FAQs
How do you calculate surface roughness? Surface roughness is typically measured using a profilometer or surface roughness tester. It’s not calculated but measured directly. The instrument traces the surface profile and provides values such as Ra (arithmetical mean roughness), Rz (maximum height of the profile), Rt (total roughness), etc.
What is 0.8 μm RA? 0.8 μm Ra (micrometers) represents the arithmetical mean roughness, which indicates the average deviation of the surface profile from a mean line over a specified measurement length. It’s a measure of the surface’s smoothness, with lower values indicating smoother surfaces.
What is 6.3 surface finish equivalent to? 6.3 is a common surface finish designation, often specified as “6.3 μm Ra” or “6.3 microinches Ra.” This surface finish level is moderate and indicates a moderately smooth surface.
What is a 250 surface finish? “250” typically refers to a surface finish in microinches, so “250 surface finish” means a surface with an average roughness of 250 microinches Ra.
What is 32 RA surface finish? “32 Ra” means an average roughness of 32 micrometers (μm). This represents a relatively rough surface.
What is a good RA value? A “good” Ra value depends on the specific application and requirements. In general, a lower Ra value indicates a smoother surface. For many industrial applications, Ra values ranging from 0.2 μm to 1.6 μm are considered good.
How do you measure RA value? Ra is measured using a profilometer or surface roughness tester. The instrument scans the surface and calculates the arithmetical mean roughness over a specified length.
What is a 125 surface finish in RA? “125 surface finish” likely refers to an Ra value of 125 microinches or 3.2 micrometers. It indicates a moderately smooth surface.
What unit is RA measured in? Ra is typically measured in micrometers (μm) or microinches (μin).
What is a 30 RA finish? A “30 RA finish” typically means an average roughness of 30 microinches Ra, indicating a moderately smooth surface.
What is 0.4 RA value? 0.4 Ra represents an average roughness of 0.4 micrometers or approximately 16 microinches. It indicates a very smooth surface.
What is RA value in microns? Ra values are measured in micrometers (μm), which are also referred to as microns.
What is 180 grit surface finish? “180 grit” is a reference to a type of abrasive material used for surface finishing. It does not directly correspond to an Ra value. The surface finish achieved with 180 grit abrasives would depend on the material and the grinding process.
What is no 4 surface finish? No. 4 surface finish is a common designation for a brushed or satin finish. It has a specific appearance characterized by fine parallel lines. The Ra value for a No. 4 finish can vary but is often around 0.4 to 0.8 micrometers.
What is a #7 finish? A #7 finish is a high-polish surface finish typically achieved through polishing processes. The Ra value for a #7 finish is generally very low, often below 0.2 μm.
What is the 16 rule for surface roughness? The “16 rule” suggests that the Ra value (average roughness) should not exceed 16 times the thickness of the gasket or sealing material when considering sealing surfaces. It’s a guideline for ensuring effective sealing.
What is 20 ra surface finish? A “20 Ra surface finish” refers to an average roughness of 20 micrometers or microns. It indicates a moderately rough surface.
What is the ASME standard for surface finish? ASME B46.1 is the American Society of Mechanical Engineers (ASME) standard for surface texture (surface roughness) measurement.
What is the RA value for grinding? The Ra value for a ground surface can vary widely depending on the grinding process and the material being ground. It may range from a few micrometers to tens of micrometers.
What is the difference between surface finish and surface roughness? Surface finish refers to the overall quality and appearance of a surface, including factors like smoothness, texture, and reflectivity. Surface roughness, on the other hand, specifically measures the small-scale deviations or irregularities on the surface.
What is the RA value of rubber? The Ra value of rubber can vary depending on the type of rubber, its manufacturing process, and its intended use. It may range from a few micrometers to tens of micrometers.
What is the typical roughness value? The typical roughness value varies widely depending on the material and application. It can range from less than 0.1 μm for highly polished surfaces to several micrometers for rougher surfaces.
What is the average roughness? Average roughness, denoted as Ra, is the arithmetical mean of the absolute values of the roughness profile deviations from the mean line within a specified measurement length.
What does a high RA value mean? A high Ra value indicates a rougher surface with larger deviations from the mean line. It implies a less smooth surface finish.
What does a 63 surface finish mean? A “63 surface finish” likely refers to an Ra value of 63 micrometers (μm). It represents a relatively rough surface.
What is the RA value of smooth finish? A smooth finish may have a very low Ra value, often below 0.2 μm.
What are the two most common methods for measuring surface finish? The two most common methods for measuring surface finish are contact profilometry (using a profilometer) and non-contact optical profilometry (using optical instruments).
What is the ISO standard for surface roughness? ISO 4287 is the ISO standard for surface texture (surface roughness) measurement.
What is the difference between RA and SA roughness? RA (arithmetical mean roughness) and SA (spatial average) are similar but differ in the calculation method. RA is calculated as the average of the absolute values of deviations within a specific sampling length, while SA considers a wider spatial area and is less sensitive to short wavelength irregularities.
What RA is 120 grit? The Ra value for a 120 grit surface finish can vary depending on the material and the grinding process, but it may be around 1-2 micrometers.
What does 20 RA mean? A “20 RA” means an average roughness of 20 micrometers or microns.
How many microns is a thickness? A micron (μm) is a unit of length equal to one millionth of a meter. When measuring thickness, it is often expressed in micrometers (microns).
What is the difference between grit and surface finish? “Grit” refers to the size of abrasive particles used in processes like sanding or grinding. “Surface finish” refers to the quality and smoothness of a surface after it has undergone a finishing process, which may involve abrasives of various grit sizes.
How many microns is 120 grit? The size of abrasive particles in 120 grit sandpaper or grinding material can vary, but it’s typically in the range of 105 to 150 microns.
Which is rougher 80 grit or 120? 80 grit is rougher than 120 grit. Smaller grit numbers indicate coarser abrasive particles, resulting in a rougher surface finish.
Will 120 grit give a smooth finish? A 120 grit abrasive can give a relatively smooth finish, especially when compared to coarser grits. However, the smoothness achieved will also depend on the material being worked on and the finishing process used.
What is a #8 finish? A #8 finish is a high-polish stainless steel finish that provides a mirror-like appearance. It has a very low Ra value, often below 0.2 μm.
What is a #6 finish? A #6 finish is a satin or brushed stainless steel finish with visible parallel lines. Its Ra value is typically around 0.4 to 0.8 μm.
What is the difference between 2B and #4 finish? 2B and #4 finishes are both stainless steel finishes, but 2B is smoother and shinier than #4. 2B has a lower Ra value, often below 0.2 μm, while #4 has a Ra value of around 0.4 to 0.8 μm and exhibits visible parallel lines.
What is a 689 finish? A “689 finish” is not a standard surface finish designation in common use. Surface finish designations typically consist of numbers, such as Ra values or grit sizes.
What is a number 3 finish? A number 3 finish is a semi-polished surface finish. It is smoother than a number 4 finish but not as polished as a number 7 or number 8 finish.
What is a number 2 finish? A number 2 finish is a more refined surface finish compared to lower numbers. It is often used in applications where appearance matters, such as in architectural or decorative elements. The Ra value for a number 2 finish is typically lower, often below 0.2 μm.
What is the RA value of a 4 finish? The Ra value for a number 4 finish is typically around 0.4 to 0.8 μm, indicating a moderately smooth surface with visible parallel lines.
What is 10 point average of surface roughness? The 10-point average roughness (Rz) is the average of the absolute values of the five highest peaks and the five deepest valleys in the roughness profile within a specified measurement length. It provides a measure of the overall roughness of the surface.
What is Max rule in surface roughness? The Maximum Material Condition (MMC) rule in surface roughness refers to specifying the maximum allowable limit for the surface roughness parameter (e.g., Ra) on a part or component. It ensures that the part’s surface does not exceed a certain level of roughness.
What is RA vs RC surface finish? RA (arithmetical mean roughness) and RC (centerline average roughness) are different parameters used to measure surface roughness. RA measures the average of the absolute values of deviations from the mean line, while RC measures the average of deviations from the centerline (midpoint between the highest peak and deepest valley).
What is difference between ASTM and ASME? ASTM (American Society for Testing and Materials) and ASME (American Society of Mechanical Engineers) are two distinct organizations that develop and publish standards. ASTM primarily focuses on materials and testing standards, while ASME develops standards primarily related to mechanical engineering and pressure vessel design.
What is standard steel surface roughness? Standard steel surface roughness can vary depending on the type of steel, manufacturing process, and application. Common Ra values for standard steel surfaces may range from 0.2 to 3.2 micrometers (μm).
Is ASME the same as ISO? No, ASME (American Society of Mechanical Engineers) and ISO (International Organization for Standardization) are separate organizations that develop different sets of standards. ASME standards are widely used in the United States, while ISO standards are recognized and used internationally.
What is the tolerance for surface grinding? Tolerance for surface grinding refers to the allowable deviation from the specified dimensions on the finished surface. It can vary depending on the specific requirements of the part or component being ground.
How much allowance should be left on a surface for grinding? The allowance left on a surface for grinding depends on the desired final dimensions, material properties, and the grinding process. It’s typically specified in engineering drawings or manufacturing instructions.
What is the formula for grinding ratio? The grinding ratio is the volume of material removed divided by the volume of grinding wheel wear. The formula for the grinding ratio is: Grinding Ratio = Volume of Material Removed / Volume of Grinding Wheel Wear
What is 0.8 RA surface finish? 0.8 Ra represents an average roughness of 0.8 micrometers or approximately 32 microinches. It indicates a relatively smooth surface.
What are the 4 types of surface texture? The four types of surface texture are roughness, waviness, lay, and flaws. These factors collectively contribute to the overall texture or appearance of a surface.
What is surface roughness for dummies? Surface roughness, in simple terms, refers to the texture or irregularities on the surface of an object. It is measured to quantify how smooth or rough a surface is and is important in various industries to ensure product quality and performance.
What happens if RA factor is very high? If the Ra factor (average roughness) is very high, it indicates a very rough surface with large deviations from a smooth and flat profile. This could be undesirable in many applications, such as precision engineering or where good sealing is required.
What is the normal range for RA investigation? The normal range for Ra investigation depends on the specific application and industry standards. It can vary widely, but for many general engineering applications, Ra values between 0.2 μm and 1.6 μm are common.
What does RA factor 10 mean? An Ra factor of 10 means that the average roughness of the surface is 10 micrometers (μm). This indicates a relatively rough surface.
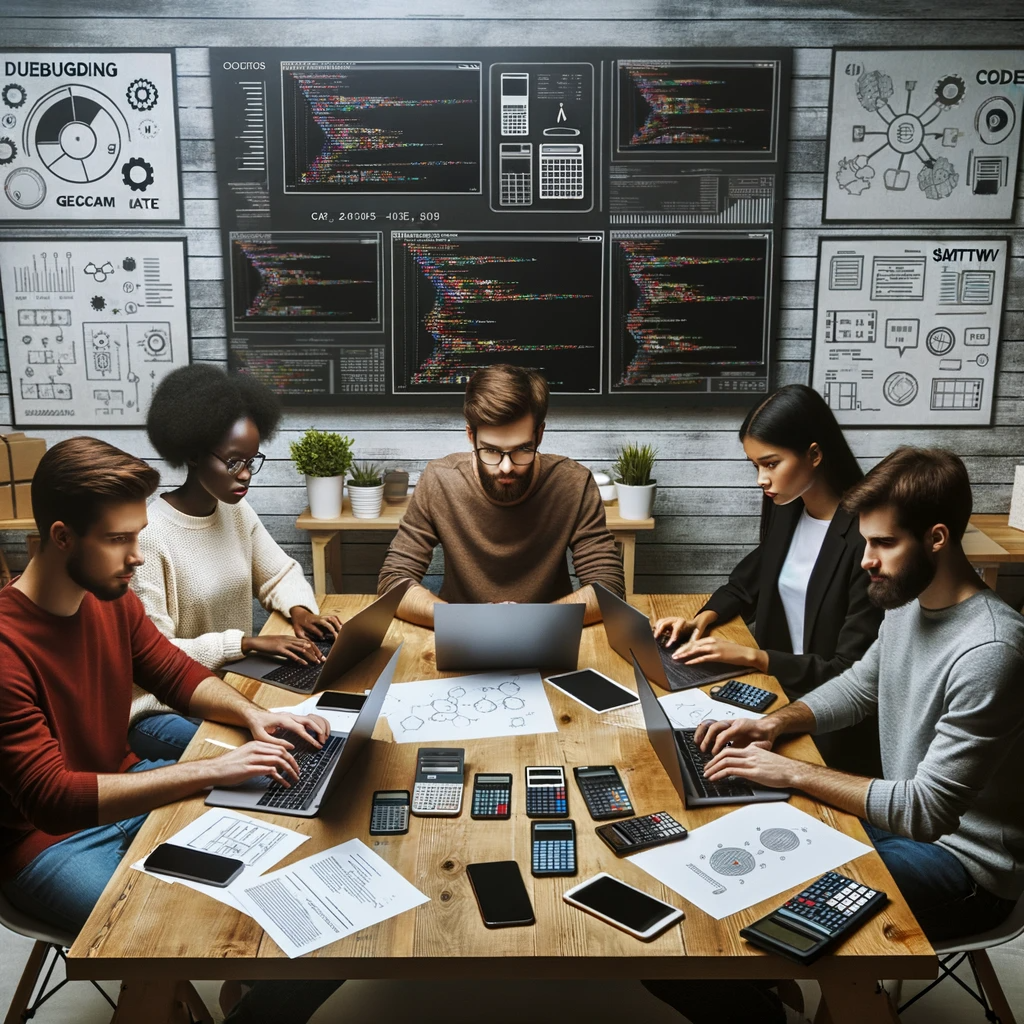
GEG Calculators is a comprehensive online platform that offers a wide range of calculators to cater to various needs. With over 300 calculators covering finance, health, science, mathematics, and more, GEG Calculators provides users with accurate and convenient tools for everyday calculations. The website’s user-friendly interface ensures easy navigation and accessibility, making it suitable for people from all walks of life. Whether it’s financial planning, health assessments, or educational purposes, GEG Calculators has a calculator to suit every requirement. With its reliable and up-to-date calculations, GEG Calculators has become a go-to resource for individuals, professionals, and students seeking quick and precise results for their calculations.