Powder Coating Coverage Calculator
Key Takeaways:
- Proper powder coating coverage is essential for achieving a flawless finish
- Understanding the basics of the powder coating application process is crucial for optimizing coverage
- Tips such as selecting the right powder and employing proper application techniques can help you achieve full coverage
- Common challenges like orange peel and pinholes can be overcome with troubleshooting techniques
- Maximizing efficiency and reducing waste in powder coating projects can result in cost savings without compromising quality
Understanding Powder Coating
Before diving into the specifics of powder coating coverage, it’s essential to understand the basics of the powder coating application process. Powder coating is a popular finishing technique that provides a durable and attractive finish to various materials. It involves applying a dry powder to a surface and then curing it to create a hard and protective coating.
The application process of powder coating includes several key considerations that directly impact the coverage and overall quality of the finish. Let’s explore these factors in more detail:
Material Preparation
Proper material preparation is crucial to achieving optimal coverage. The surface must be thoroughly cleaned and free from contaminants such as dirt, oil, rust, or old paint. Any imperfections or irregularities on the surface should be addressed, as they can affect the adhesion of the powder coating and result in uneven coverage.
Application Methods
There are different methods available for applying powder coating, including electrostatic spray, fluidized bed, and powder flocking. The choice of application method depends on the nature of the material, the desired finish, and the equipment available. Each method has its own advantages and considerations, which can impact the coverage and overall results.
Thickness
Proper thickness is essential for achieving good coverage and ensuring the durability of the powder coating. The coating thickness can vary depending on the material, application method, and required performance. It is crucial to follow the manufacturer’s recommendations and industry standards to achieve the desired coverage and ensure the coating’s effectiveness.
By understanding these key considerations in the powder coating application process, you can make informed decisions to achieve the best possible coverage in your projects. In the next section, we will explore practical tips for achieving full coverage and ensuring a flawless finish.
Tips for Achieving Full Coverage
When it comes to powder coating projects, achieving full coverage is essential for ensuring a flawless finish. To help you achieve optimal results, we’ve compiled a list of practical tips and techniques. From selecting the correct powder for your substrate to using proper application methods, these insights will guide you towards achieving full coverage and a stunning end product.
1. Understand Your Substrate
Before starting any powder coating project, it’s crucial to understand the characteristics of your substrate. Different materials may require specific preparation techniques to achieve proper adhesion and full coverage. Conduct thorough research or consult with coating experts to determine the best approach for your specific substrate.
2. Choose the Right Powder
Selecting the correct powder for your project is vital to ensure full coverage. Consider factors such as color, texture, and durability when choosing your powder. Additionally, opt for powders that offer good coverage capabilities, ensuring that a single coat is sufficient for achieving the desired finish.
3. Proper Preparation Is Key
Proper surface preparation is crucial for achieving full coverage with powder coating. Ensure that the substrate is clean, free from debris, grease, and oxidation. This will help the powder adhere evenly and prevent any issues with coverage or adhesion.
4. Use Proper Application Techniques
Applying powder coatings requires careful attention to technique. Consider the following tips:
- Use a spray gun with adjustable settings to control the flow and pattern of the powder.
- Ensure the gun is held at the correct distance from the substrate for ideal coverage.
- Apply the powder evenly and avoid excessive buildup in certain areas.
- Consider using a back-forth or crisscross motion to prevent streaks or uneven coverage.
5. Pay Attention to Curing Temperature and Time
Curing the powder coating at the proper temperature and for the right duration is essential for achieving full coverage and a durable finish. Follow the manufacturer’s instructions for the recommended curing temperature and time to ensure optimal results.
Pro Tip: Conduct a test sample or small-scale trial before coating larger surfaces to ensure proper coverage, adhesion, and curing.
By following these tips, you can enhance your powder coating skills and achieve full coverage in your projects. Remember, attention to detail and proper technique are key to achieving a flawless finish that will impress clients and stand the test of time.
Overcoming Common Coverage Challenges
Despite your best efforts, achieving perfect powder coating coverage can sometimes present challenges. Understanding and troubleshooting these common issues is key to attaining a flawless finish. In this section, we will address three of the most prevalent coverage challenges: orange peel, pinholes, and coverage inconsistencies. By exploring practical solutions and troubleshooting tips, you’ll be equipped to overcome these obstacles and achieve the desired results in your powder coating projects.
Orange Peel
Orange peel refers to a textured and uneven surface appearance that resembles the peel of an orange. It typically occurs due to improper powder coating application techniques, inadequate powder flow, or incorrect curing temperatures.
To overcome orange peel challenges, consider the following troubleshooting tips:
- Ensure proper grounding of the workpiece and the coating equipment to prevent excess static charge.
- Adjust the gun settings, such as the powder flow rate and electrostatic voltage, to optimize coating deposition.
- Verify that the curing oven temperature and duration are within the specified manufacturer’s guidelines for the powder coating material.
Pinholes
Pinholes are small, unintended holes or voids in the powder coating film that compromise coverage and can lead to corrosion or other damage over time. They are typically caused by surface contaminants, inadequate pretreatment, or improper powder application techniques.
To troubleshoot and minimize pinholes, consider the following tips:
- Thoroughly clean and prepare the substrate surface before applying the powder coating to remove any contaminants or residues.
- Ensure proper grounding to minimize the occurrence of electrostatically charged particles that can create pinholes.
- Optimize powder application techniques, such as adjusting the gun settings, powder flow, and spray distance, to achieve a uniform and complete coating.
Coverage Inconsistencies
Coverage inconsistencies refer to variations in the thickness or uniformity of the powder coating film across the workpiece. They can result from factors such as improper pre-cleaning, incorrect powder selection, or inadequate application techniques.
To address coverage inconsistencies, consider the following troubleshooting measures:
- Thoroughly clean the substrate and ensure it is free from dust, oils, or other contaminants before applying the powder coating.
- Select the appropriate powder coating material that matches the substrate and application requirements to achieve optimal coverage and adhesion.
- Ensure proper gun-to-substrate distance, powder flow rate, and electrostatic voltage to achieve a uniform and consistent coating thickness.
Common Coverage Challenges | Troubleshooting Tips |
---|---|
Orange Peel | Adequate grounding, proper gun settings, and correct curing temperatures. |
Pinholes | Thorough cleaning, proper grounding, and optimized powder application techniques. |
Coverage Inconsistencies | Effective pre-cleaning, appropriate powder selection, and precise application techniques. |
Maximizing Efficiency and Reducing Waste
In powder coating projects, maximizing efficiency and reducing waste are critical goals for achieving cost savings without compromising on quality. By implementing strategic strategies, you can optimize coverage, minimize overspray and material waste, and reduce energy consumption. Let’s explore some effective techniques:
1. Suitable Equipment and Settings
Investing in high-quality powder coating equipment and ensuring proper equipment calibration can significantly improve efficiency and waste reduction. Select equipment that offers precise control over powder application, such as adjustable gun settings and variable voltage controls. Use equipment specifically designed for efficient powder transfer and uniform coverage.
2. Proper Training and Technique
Providing comprehensive training to operators on powder coating application techniques is essential for maximizing efficiency. Educate your team on efficient powder coating methods, such as using the correct gun-to-part distance, maintaining consistent gun movement, and achieving proper grounding for electrostatic attraction. Implementing best practices will help minimize overspray and ensure accurate powder deposition.
3. Optimal Application Process
Strategically plan your powder coating process to achieve maximum efficiency. Consider factors such as batch size, order of parts, and application sequence. By organizing parts efficiently, you can minimize setup time, reduce material wastage, and streamline the overall process.
4. Efficient Powder Recovery Systems
Implementing effective powder recovery systems can significantly reduce waste and improve efficiency. Invest in technologies such as powder booths, filters, and reclaim systems that capture, filter, and recirculate excess powder for reuse. This way, you can reduce material waste and minimize the amount of powder that is lost during the coating process.
5. Continuous Improvement and Optimization
Regularly evaluate and refine your powder coating processes to identify areas for improvement. Conduct thorough inspections to identify potential sources of waste or inefficiencies, such as inadequate material preparation, excessive overspray, or improper equipment maintenance. Implement corrective actions to optimize the process and achieve higher efficiency and waste reduction.
By implementing these strategies, you can maximize efficiency, reduce waste, and improve powder coating coverage. Not only will this result in cost savings for your projects, but it will also help maintain a sustainable and environmentally conscious approach to powder coating.
Benefits of Maximizing Efficiency and Reducing Waste: |
---|
1. Cost savings through reduced material waste |
2. Improved productivity and faster turnaround times |
3. Enhanced environmental sustainability |
4. Consistent and high-quality powder coating coverage |
Conclusion
In conclusion, powder coating coverage plays a crucial role in achieving a flawless finish for your projects. Throughout this article, we have explored the key factors and techniques that can help you unlock optimal results. By implementing the insights shared, you can ensure that your powder coating projects meet the highest standards of quality and durability.
One of the main takeaways from this discussion is the importance of thorough material preparation. By properly cleaning and treating the substrate, you can create an ideal surface for the powder coating to adhere to, enhancing coverage and reducing the risk of adhesion issues.
Additionally, adopting the right application techniques and using the correct powder for your specific substrate can significantly impact coverage. Selecting the appropriate thickness and ensuring an even distribution of the powder will help achieve full coverage without excessive overspray or material waste.
Remember, achieving flawless coverage is not without its challenges. Factors such as orange peel, pinholes, and inconsistencies may arise. However, armed with the troubleshooting tips and solutions discussed in this article, you can overcome these challenges and achieve the desired results.
FAQ
What is powder coating coverage and why is it important?
Powder coating coverage refers to the extent to which the powder coating material spreads and adheres to the substrate surface. It is important because it directly impacts the appearance, durability, and performance of the finished coating. Insufficient coverage can result in a compromised finish with visible blemishes and reduced protection against corrosion and wear.
What factors affect powder coating coverage?
Several factors can influence powder coating coverage. These include the texture and cleanliness of the substrate, the type and quality of the powder coating material, the application method used, and the thickness of the coating. Proper consideration and optimization of these factors help achieve optimal coverage and a flawless finish.
How can I ensure full coverage in my powder coating projects?
To achieve full coverage, start by selecting the appropriate powder coating material for your specific substrate. Ensure proper surface preparation, including cleaning and degreasing, to enhance adhesion. Use appropriate application techniques, such as electrostatic spraying or fluidized bed dipping, to evenly disperse the powder. Finally, measure and control the coating thickness to ensure adequate coverage.
What are some common challenges related to powder coating coverage?
Common challenges in powder coating coverage include the occurrence of orange peel texture, pinholes, and inconsistencies in coverage thickness. Orange peel refers to a bumpy or wrinkled surface texture, while pinholes are small, punctured areas in the coating. Inconsistent thickness can result in uneven coverage. Understanding the causes of these challenges and implementing proper troubleshooting techniques can help overcome them.
How can I maximize efficiency and reduce waste in powder coating projects?
Efficiency and waste reduction can be achieved through careful planning and optimization. Use the right equipment and techniques to minimize overspray and ensure accurate powder application. Implement a proper reclaim system to collect and reuse excess powder. Additionally, optimize curing processes and minimize energy consumption. By doing so, you can maximize cost savings while maintaining high-quality powder coating coverage.
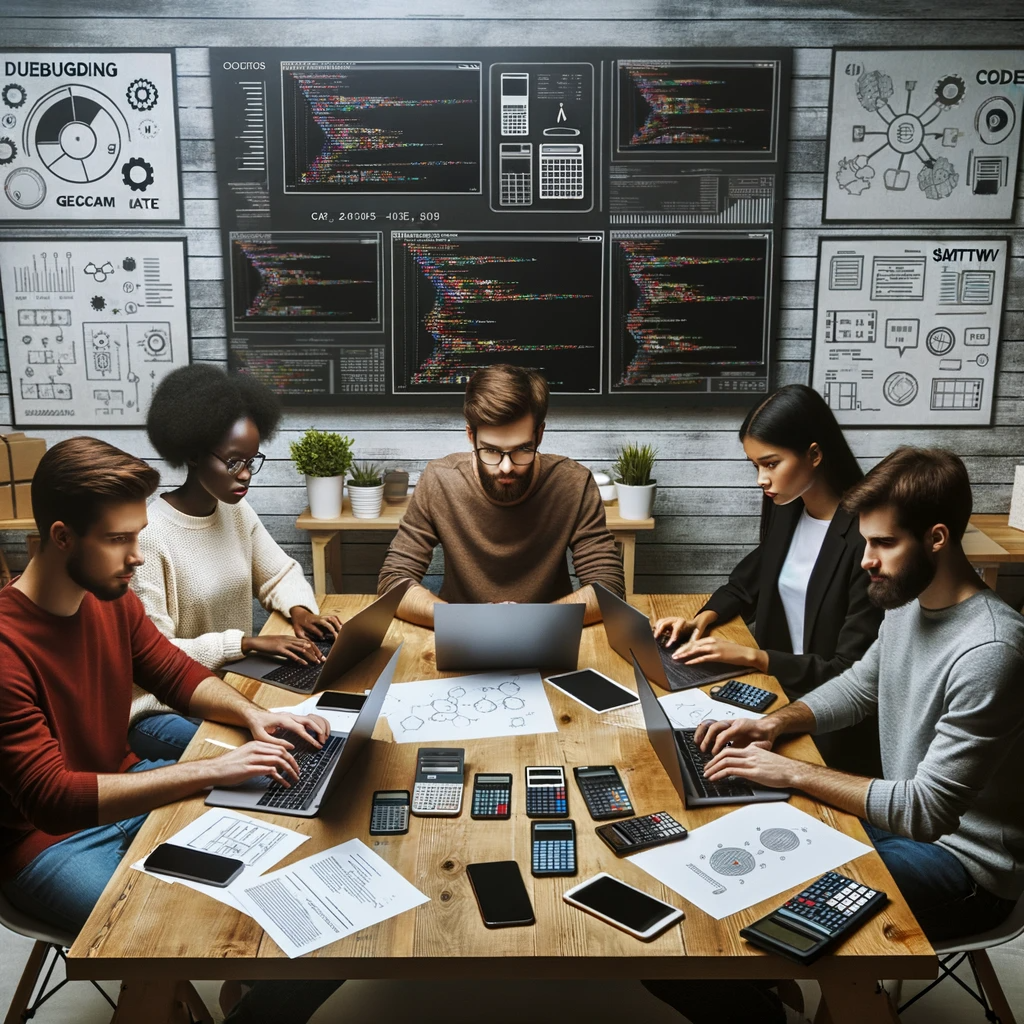
GEG Calculators is a comprehensive online platform that offers a wide range of calculators to cater to various needs. With over 300 calculators covering finance, health, science, mathematics, and more, GEG Calculators provides users with accurate and convenient tools for everyday calculations. The website’s user-friendly interface ensures easy navigation and accessibility, making it suitable for people from all walks of life. Whether it’s financial planning, health assessments, or educational purposes, GEG Calculators has a calculator to suit every requirement. With its reliable and up-to-date calculations, GEG Calculators has become a go-to resource for individuals, professionals, and students seeking quick and precise results for their calculations.