Degree Chamfer Calculator
Chamfer Width:
Chamfer Depth:
Certainly, here’s a table showing chamfer angles ranging from 0 to 120 degrees:
Chamfer Angle (Degrees) |
---|
0 |
10 |
20 |
30 |
40 |
50 |
60 |
70 |
80 |
90 |
100 |
110 |
120 |
This table includes increments of 10 degrees from 0 to 120 degrees for chamfer angles.
FAQs
How do you calculate the depth of a chamfer? The depth of a chamfer is typically specified in engineering drawings. It is the distance from the original edge or surface to the furthest point of the chamfer along the beveled surface. You can measure it directly using a ruler or caliper.
How do you calculate a 82-degree countersink? To create an 82-degree countersink, you need to calculate the angle between the original surface and the tapered countersink. You can use trigonometry to do this. The formula is:
Countersink Angle=arctan(Chamfer Diameter2×Depth of Countersink)Countersink Angle=arctan(2×Depth of CountersinkChamfer Diameter)
How do you calculate countersink size? Countersink size is typically specified as the diameter of the larger circle created by the conical or tapered surface of the countersink. You can measure it directly with a ruler, caliper, or by referring to engineering drawings.
What does 45-degree chamfer mean? A 45-degree chamfer means that the beveled edge or surface forms a 45-degree angle with the original surface. It’s a common chamfer angle used in various applications.
What is the standard depth of a chamfer? The standard depth of a chamfer can vary depending on the application and industry standards. However, a common depth for chamfers is often specified as 1/32 to 1/8 inch (0.8 to 3.2 millimeters).
What does a 90-degree countersink mean? A 90-degree countersink means that the angle between the original surface and the tapered countersink surface is 90 degrees. In other words, it creates a right angle.
What is a 100-degree countersink used for? A 100-degree countersink is used when a shallower angle is needed compared to the more common 82-degree countersink. It is often used in specialized applications where a very gradual taper is required.
What is the general rule of countersink? The general rule for countersinking is to create a conical or tapered recess in a material to accommodate the head of a screw or bolt, allowing it to sit flush with or below the surface. The countersink should match the angle and size of the fastener head being used.
What is the chamfer angle for a countersink? The chamfer angle for a countersink can vary, but a common angle is 45 degrees. However, it can be different depending on the specific application and requirements.
What are the 4 most common countersink angles? The four most common countersink angles are 82 degrees, 90 degrees, 100 degrees, and 120 degrees. These angles are often used in various engineering and manufacturing applications.
What is the angle of a countersunk screw chamfer? The angle of a countersunk screw chamfer is typically 82 degrees, but it can vary depending on the design and application.
What is the difference between a chamfer and a countersink? A chamfer is a beveled edge or surface that does not necessarily create a recess for a screw or bolt head. A countersink, on the other hand, is a type of chamfer specifically designed to create a conical or tapered recess to accommodate a fastener head.
What size is a #10 countersink? The size of a #10 countersink can vary depending on the specific design and manufacturer, but it is typically designed to accommodate a #10 screw, which has a major diameter of 0.190 inches (4.83 millimeters).
What size is a number 8 countersink? A number 8 countersink is designed to accommodate a #8 screw, which has a major diameter of 0.164 inches (4.17 millimeters).
Is a chamfer always cut at 45 degrees? No, a chamfer is not always cut at 45 degrees. The angle of a chamfer can vary depending on the specific requirements of the design and application.
How do you measure the angle of chamfer? You can measure the angle of a chamfer using a protractor or an angle measuring tool. Place the tool along the chamfered edge or surface to determine the angle.
What is the difference between a chamfer and an edge? A chamfer is a specific type of beveled edge or surface, while an edge refers to any border or boundary of an object. Chamfers are typically created intentionally for design or functional purposes.
What size is a C3 chamfer? The designation “C3” alone does not specify a chamfer size. Chamfer sizes are typically defined by their dimensions, such as the depth and width, or by angles.
What is the tolerance for chamfer dimensions? The tolerance for chamfer dimensions can vary depending on the specific application and industry standards. Tolerances are often specified in engineering drawings and can range from a few thousandths of an inch to larger values, depending on the precision required.
What is the difference between a chamfer and a bevel? Chamfer and bevel are often used interchangeably, but in some contexts, a chamfer is a beveled edge or surface with a specific angle, while a bevel can refer to any sloped or angled edge or surface without specifying a particular angle.
What is the best angle for chamfer? The best angle for a chamfer depends on the specific application and design requirements. Common chamfer angles include 45 degrees, 30 degrees, and 60 degrees, but the choice of angle should be based on functional and aesthetic considerations.
How do you calculate countersink depth? Countersink depth is the distance from the original surface to the deepest point of the tapered recess. It is specified in engineering drawings and can be measured directly using a ruler or caliper.
Does a chamfer have teeth or threads? A chamfer does not have teeth or threads. It is a beveled edge or surface created by cutting or shaping the material at an angle.
What are 60-degree countersinks used for? 60-degree countersinks are often used in applications where a shallower angle is needed compared to the more common 82-degree countersink. They may be used for securing components where a flush fit is not required.
What is standard countersink angle? The standard countersink angle is often 82 degrees, but other angles like 90 degrees, 100 degrees, and 120 degrees are also common, depending on the application.
What is the minimum countersink depth? The minimum countersink depth is typically specified in engineering drawings and can vary depending on the specific application. There is no universal minimum depth, as it depends on the size and type of fastener being used.
What’s the difference between countersink and double countersunk? A countersink creates a single tapered recess for a fastener head, while a double countersink creates two tapered recesses, typically opposite each other, to accommodate two fastener heads.
What are the two most often used angles in countersink holes? The two most often used angles in countersink holes are 82 degrees and 90 degrees. These angles are commonly used to accommodate various types of fasteners.
How do you countersink without a countersink bit? You can countersink without a countersink bit by using a larger drill bit or a specialized hand tool like a countersink tool. By carefully controlling the angle and depth of the tool, you can create a countersink.
Do you countersink before or after tapping? Countersinking is typically done before tapping. Countersinking creates a recess for the fastener head, allowing it to sit flush with or below the surface. After countersinking, you can then tap the hole to create threads for the screw or bolt.
How close can a countersink be to an edge? The distance between a countersink and an edge should be specified in engineering drawings and can vary depending on the application and material. It is essential to maintain a sufficient distance to ensure the integrity and strength of the material around the countersink.
Why are countersinks 82 degrees? 82-degree countersinks are common because they provide a good compromise between creating a recess for the fastener head and maintaining adequate material thickness around the hole. This angle allows for secure fastening while minimizing the weakening of the material.
Can you chamfer with a countersink? Yes, you can use a countersink tool to create a chamfer by adjusting the tool’s depth and angle. However, the primary purpose of a countersink tool is to create a conical recess for a fastener head.
Can countersinking create a chamfer? Yes, countersinking can create a chamfer, as the process involves beveling or tapering the edge or surface of the material to accommodate a fastener head. The chamfer is essentially a byproduct of the countersinking process.
What is the standard angle for a flat head countersink? The standard angle for a flat head countersink is often 82 degrees, but other angles may also be used depending on the specific design and application.
What is the standard included angle on a countersink for an inch-sized flat head cap screw? The standard included angle for a countersink to accommodate an inch-sized flat head cap screw is typically 82 degrees. This angle is commonly used for such fasteners.
What is the angle on a woodscrew? The angle on a woodscrew typically refers to the thread angle. It can vary, but a common thread angle for wood screws is around 60 degrees. This angle helps the screw penetrate and grip wood effectively.
How do you chamfer a screw hole? To chamfer a screw hole, you can use a countersink tool or a chamfering tool. Simply place the tool in the hole and rotate it to create a beveled edge around the opening, allowing the screw to enter smoothly.
What is the edge distance for countersunk bolts? The edge distance for countersunk bolts refers to the minimum distance between the center of the countersunk hole and the edge of the material. The specific edge distance may vary depending on the material and design requirements but is typically specified in engineering standards and guidelines.
What is a screw chamfer? A screw chamfer refers to the beveled or tapered edge or surface around a hole designed to accommodate a screw or bolt head. It allows the screw head to sit flush with or below the surface of the material.
What is the disadvantage of chamfer? One potential disadvantage of chamfers is that they remove material, which can weaken the structural integrity of the part or component. Additionally, excessive chamfering can reduce the surface area available for fastening, affecting the overall strength of the connection.
What are the advantages of chamfered edges? Chamfered edges offer several advantages, including improved aesthetics, reduced sharpness and potential for injury, and enhanced ease of assembly when using fasteners. They can also help prevent chipping and delamination in materials like wood and composite.
What is another name for chamfered edge? Another name for a chamfered edge is a “beveled edge” or simply a “chamfer.” These terms are often used interchangeably to describe a beveled or tapered edge or surface.
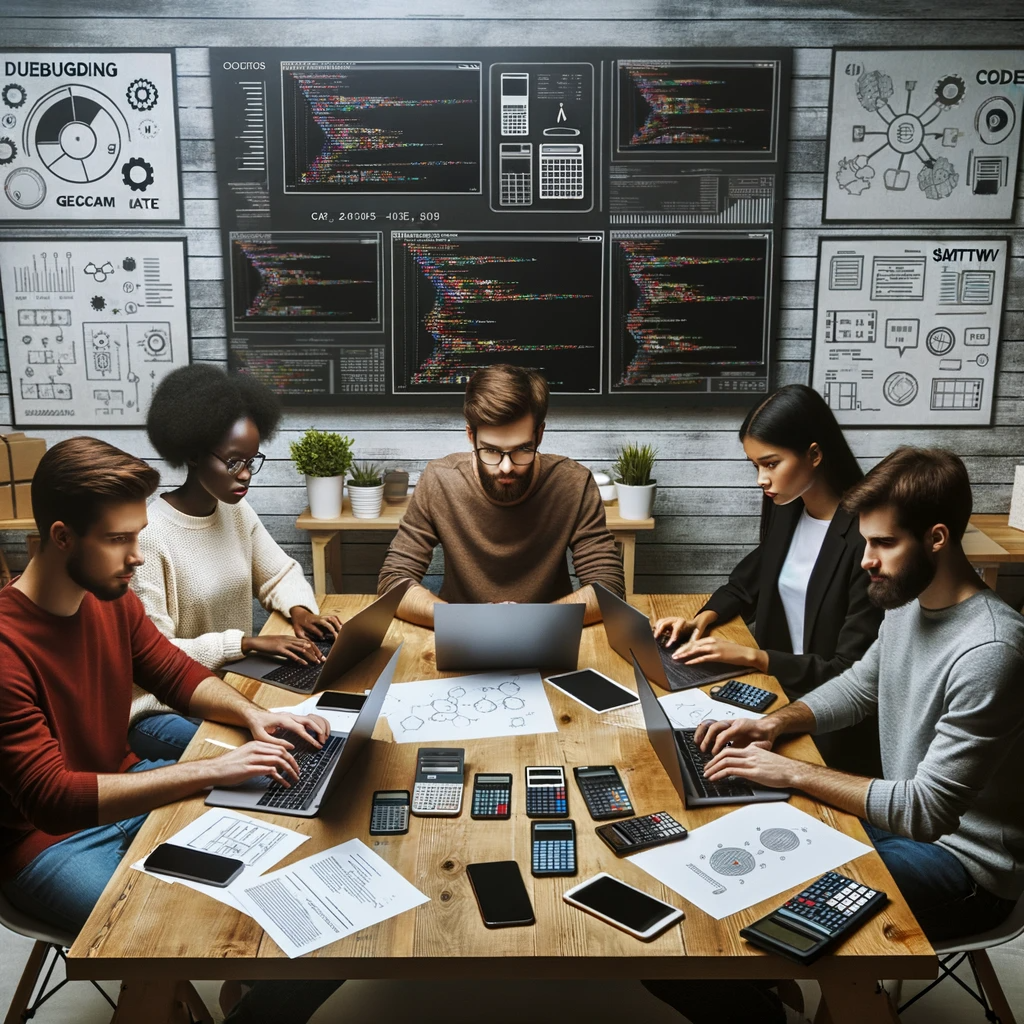
GEG Calculators is a comprehensive online platform that offers a wide range of calculators to cater to various needs. With over 300 calculators covering finance, health, science, mathematics, and more, GEG Calculators provides users with accurate and convenient tools for everyday calculations. The website’s user-friendly interface ensures easy navigation and accessibility, making it suitable for people from all walks of life. Whether it’s financial planning, health assessments, or educational purposes, GEG Calculators has a calculator to suit every requirement. With its reliable and up-to-date calculations, GEG Calculators has become a go-to resource for individuals, professionals, and students seeking quick and precise results for their calculations.