The Process Capability Index (Cp) assesses how well a process can produce items within specification limits. It is calculated by dividing the range of specification limits by six times the process’s standard deviation. A higher Cp indicates a process that is better at consistently producing products within the specified tolerances, thus exhibiting greater capability.
Process Capability Index Calculator
Certainly, here’s a simple table providing an overview of the Process Capability Index (Cp):
Term | Definition |
---|---|
Process Capability Index | A statistical measure to assess how well a process can consistently produce items within specification limits. It quantifies the capability of a process to meet customer requirements. |
Components | – USL (Upper Specification Limit): The maximum allowable value for a product’s characteristic. |
– LSL (Lower Specification Limit): The minimum allowable value for a product’s characteristic. | |
– σ (Sigma): The standard deviation of the process, indicating its variability. | |
Interpretation | – A higher Cp value suggests a more capable process. |
– Cp ≥ 1 indicates that the process spread is less than the specification width. | |
– Cp < 1 implies that the process spread exceeds the specification width, indicating potential issues. | |
Application | Used in quality control and Six Sigma methodologies to assess and improve processes. |
This table provides a concise summary of the Process Capability Index, its formula, key components, interpretation, and its application in process improvement and quality control.
FAQs
- Process Capability Index (Cp): Cp measures how well a process can produce items within specified limits. It is calculated by taking the difference between the upper specification limit (USL) and the lower specification limit (LSL) and dividing it by six times the standard deviation of the process. A higher Cp indicates a better process capability.
- Cpk Index: Cpk is another measure of process capability, but it considers both how well the process fits within the specifications and its centering (mean). It is calculated by finding the minimum of two values: (a) the difference between the mean and the nearest specification limit divided by three times the standard deviation and (b) the same calculation for the other specification limit. A higher Cpk indicates a better process.
- Good CP Value: A good Cp value is typically greater than 1. A Cp of 1 indicates that the process variability is equal to the width of the specification limits. Higher values of Cp indicate that the process has less variation relative to the specifications.
- Calculating Cpk in Excel: You can calculate Cpk in Excel by using the formula mentioned earlier for Cpk. You’ll need to input the values for USL, LSL, mean (μ), and standard deviation (σ) into your Excel spreadsheet and then use the formula to find Cpk.
- Manual Calculation of Cpk: To manually calculate Cpk, follow these steps: a. Calculate the difference between the mean and the nearest specification limit. b. Divide this difference by three times the standard deviation. c. Repeat the above two steps for the other specification limit. d. Choose the smaller of the two values obtained in steps (a) and (c) as your Cpk value.
- Good Cpk Index: A good Cpk index is generally considered to be 1.33 or higher. A Cpk of 1.33 indicates that the process is capable of producing items that meet the specifications with a margin of safety.
- Cpk 1.67: A Cpk of 1.67 indicates a process that is highly capable of producing items within the specifications with a significant margin of safety. It represents a very reliable and consistent process.
- CPK 1.5: A Cpk of 1.5 also indicates a capable process, but it has a smaller margin of safety compared to a Cpk of 1.67. It is still considered a good level of process capability.
- CP vs. Cpk: CP measures process capability without considering the centering of the process, while Cpk takes both the process spread and centering into account.
- CPK 0.67: A Cpk of 0.67 suggests that the process is not capable of consistently producing items within the specifications, and there is a high risk of producing out-of-spec products.
- Cpk Value in Six Sigma: In Six Sigma, a Cpk value of 2 or higher is often targeted as it represents a highly capable process with minimal defects.
- 1.67 Cpk and Sigma: A Cpk of 1.67 corresponds to approximately 5 Sigma capability in a process.
- 1.33 Cpk Confidence Level: A Cpk of 1.33 typically corresponds to a confidence level of about 90%.
- CP 1.50: A CP of 1.50 indicates that the process spread is 1.5 times the width of the specification limits. It measures process capability but doesn’t consider process centering.
- CP Greater Than 1: If CP is greater than 1, it suggests that the process spread is less than the width of the specification limits, indicating some level of capability.
- CP and Cpk Equality: CP and Cpk can be equal when the process is perfectly centered between the specification limits. In this case, both indices yield the same value.
- Minimum Data for Cpk Calculation: To calculate Cpk, you typically need data on process measurements, including sample size, mean, and standard deviation.
- Sample Size for Cpk Calculation: The sample size should be sufficiently large to provide a representative estimate of the process variation. A larger sample size often leads to more reliable Cpk calculations.
- Cpk of 0.5: A Cpk of 0.5 suggests that the process is not capable of consistently meeting the specifications, and there is a high likelihood of producing out-of-spec products.
- Sigma vs. Cpk: Sigma represents the standard deviation and is a measure of process variability, while Cpk is a capability index that indicates how well a process fits within specification limits and is centered.
- 3 Sigma Process Capability: A process with a capability of 3 Sigma means it can produce items with a certain level of defects, but it may not meet specifications consistently.
- High CPK: A very high Cpk value, such as 2 or greater, indicates an extremely capable process with minimal variation and a wide margin of safety within the specifications.
- CPK Too High: While a high Cpk is generally desirable, if it is excessively high, it might indicate overcontrol, which can lead to unnecessary costs.
- Normal CPK: A normal Cpk value depends on the specific industry and product, but a Cpk of 1.33 is often considered acceptable in many cases.
- Cpk of 1.11: A Cpk of 1.11 indicates a process that is capable of producing items within specifications, but it has a relatively narrow margin of safety.
- Cpk Lower than CP: If Cpk is lower than CP, it suggests that the process is not centered between the specification limits.
- CP Greater than Cpk: CP can be greater than Cpk when the process is centered between the specification limits but still has some level of variation.
- Process Capability Example: An example of process capability is a manufacturing process for screws where the specifications require a length between 2.95 inches and 3.05 inches. If the process consistently produces screws within this range, it has good process capability.
- Low CPK: A low Cpk indicates that the process is not capable of consistently meeting the specifications, and improvements may be needed to make it more capable.
- Increasing CPK: To increase Cpk, you can work on reducing process variation (lowering standard deviation) and/or improving process centering (adjusting the mean) to bring the process closer to the target value.
- Cpk 5 Sigma: A Cpk of 5 Sigma represents an exceptionally high level of process capability and corresponds to very low defect rates.
- 3 Sigma vs. 6 Sigma Cpk: A 3 Sigma process capability indicates a process with moderate capability, while a 6 Sigma process capability represents an extremely capable process with very low defect rates.
- 4 Sigma vs. 6 Sigma: A 6 Sigma process is more capable than a 4 Sigma process, indicating lower variability and fewer defects.
- 5 Sigma vs. 6 Sigma: A 6 Sigma process is even more capable than a 5 Sigma process, with fewer defects and higher consistency.
- Cpk with Standard Deviation of 0: If the standard deviation is 0, Cpk would be undefined because division by zero is not possible.
- Cpk 4 Sigma: A Cpk of 4 Sigma indicates a highly capable process with low variation and a wide margin of safety within the specifications.
- Sample Size and Cpk: A larger sample size can provide a more accurate estimate of the process standard deviation, which in turn affects the Cpk calculation. A smaller sample size may lead to less reliable Cpk values.
- CP Value of 1.33: A CP value of 1.33 indicates that the process spread is 1.33 times the width of the specification limits. It measures process capability but doesn’t consider process centering.
- CP 1.00: A CP value of 1.00 suggests that the process spread is equal to the width of the specification limits, indicating the process can meet specifications but with little margin of safety.
- High CP Value: A high CP value is generally considered good because it indicates that the process can meet specifications. However, CP alone doesn’t consider process centering.
- Interpreting CP Value: To interpret CP, compare it to the desired specifications. A CP greater than 1 suggests that the process spread is less than the specification width, while a CP less than 1 indicates that the process spread is greater than the specification width.
- Higher CP Than Water: Water, being a highly consistent substance, would have a CP value significantly greater than 1, indicating that its variability is much lower than any typical manufacturing process.
- CP Less Than CV: CP can be less than the coefficient of variation (CV) when the process is not well-centered within the specification limits.
- CP Higher Than CV for an Ideal Gas: In the case of an ideal gas, CP can be higher than CV because the process may be perfectly centered within the specification limits, resulting in a higher CP value.
- Minimum Sample Size for Process Capability: The minimum sample size for process capability calculations can vary depending on the specific industry and standards, but a sample size of 30 or more is often considered sufficient for reliable estimates.
- Increasing Process Capability: To increase process capability, focus on reducing process variation (lowering standard deviation) and ensuring that the process is well-centered within the specification limits.
- Process Not Stable: When a process is not stable, it means that it is experiencing significant variations or fluctuations, making it unpredictable and less capable of producing consistent results.
- Good CP Value: A good CP value depends on the specific industry and product, but generally, a CP greater than 1 indicates a capable process.
- Calculating Cpk in Excel: To calculate Cpk in Excel, you can use the formula mentioned earlier for Cpk. Input the values for USL, LSL, mean (μ), and standard deviation (σ) into your Excel spreadsheet, and then use the formula to find Cpk.
- Calculating CP and Cpk with Example: Here’s a simplified example: Suppose you have a process to produce widgets with a target length of 10 inches, a tolerance of ±0.2 inches (LSL = 9.8 inches, USL = 10.2 inches), a mean length of 10 inches (μ), and a standard deviation of 0.1 inches (σ).
- Calculate CP: (USL – LSL) / (6 * σ) = (10.2 – 9.8) / (6 * 0.1) = 0.67
- Calculate Cpk: Min((USL – μ) / (3 * σ), (μ – LSL) / (3 * σ)) = Min((10.2 – 10) / (3 * 0.1), (10 – 9.8) / (3 * 0.1)) = Min(0.67, 0.67) = 0.67 In this example, CP and Cpk are both 0.67, indicating that the process is capable but not centered within the specifications.
- Calculating CPK on Non-Normal Data: While CPK calculations are typically based on normal distribution assumptions, they can still provide useful insights for non-normal data. However, for non-normal data, it’s important to assess the distribution and consider transformation techniques or non-parametric methods for a more accurate analysis.
- Calculate CP and Cpk in Excel: To calculate CP and Cpk in Excel, you can use the formulas provided earlier and input your data into Excel cells. For example, you can use cell references for USL, LSL, mean, and standard deviation in the formulas to perform the calculations. Excel functions like STDEV.P can help calculate standard deviation.
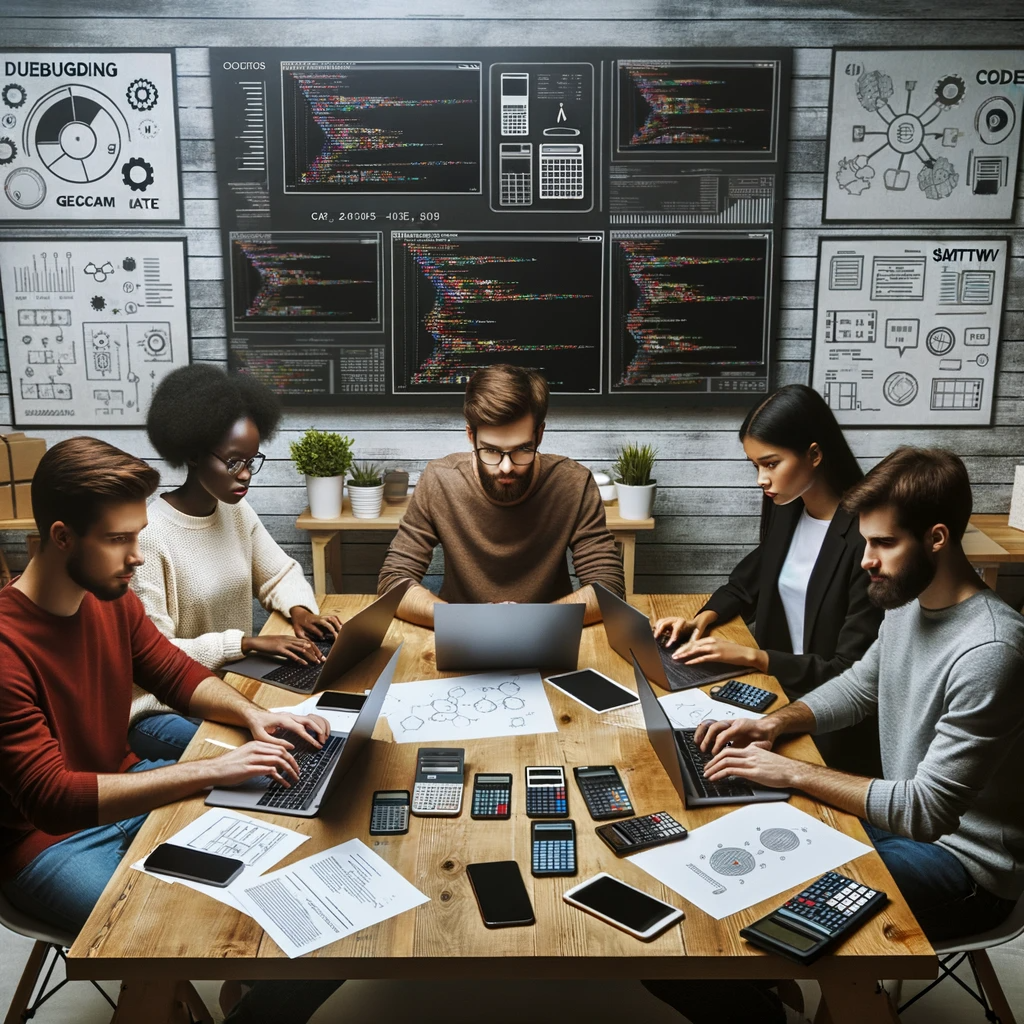
GEG Calculators is a comprehensive online platform that offers a wide range of calculators to cater to various needs. With over 300 calculators covering finance, health, science, mathematics, and more, GEG Calculators provides users with accurate and convenient tools for everyday calculations. The website’s user-friendly interface ensures easy navigation and accessibility, making it suitable for people from all walks of life. Whether it’s financial planning, health assessments, or educational purposes, GEG Calculators has a calculator to suit every requirement. With its reliable and up-to-date calculations, GEG Calculators has become a go-to resource for individuals, professionals, and students seeking quick and precise results for their calculations.