Tolerance stack-up analysis assesses the cumulative impact of component tolerances in an assembly. It ensures that the assembled product functions correctly within specified limits. By calculating the worst-case or statistical outcomes, engineers can determine if the assembly meets design requirements and make necessary adjustments to control variations and ensure product quality.
Tolerance Stack-Up Calculator
Tolerance Values:
Component | Dimension (mm) | Tolerance (mm) | Upper Limit (mm) | Lower Limit (mm) |
---|---|---|---|---|
A | 100.00 | ±0.05 | 100.05 | 99.95 |
B | 50.00 | ±0.03 | 50.03 | 49.97 |
C | 75.00 | ±0.02 | 75.02 | 74.98 |
D | 30.00 | ±0.04 | 30.04 | 29.96 |
Total Stack-Up |
In this example:
- Component A has a dimension of 100.00 mm with a tolerance of ±0.05 mm, resulting in an upper limit of 100.05 mm and a lower limit of 99.95 mm.
- Component B has a dimension of 50.00 mm with a tolerance of ±0.03 mm, resulting in an upper limit of 50.03 mm and a lower limit of 49.97 mm.
- Component C has a dimension of 75.00 mm with a tolerance of ±0.02 mm, resulting in an upper limit of 75.02 mm and a lower limit of 74.98 mm.
- Component D has a dimension of 30.00 mm with a tolerance of ±0.04 mm, resulting in an upper limit of 30.04 mm and a lower limit of 29.96 mm.
To calculate the total stack-up for this assembly, you can use the tolerance stack-up analysis methods mentioned earlier, such as worst-case analysis or Root Sum Square (RSS) analysis. Once you’ve determined the total stack-up, you can fill in the “Total Stack-Up” row in the table with the appropriate values.
FAQs
How do you calculate stack up tolerance? To calculate stack-up tolerance, you need to consider the cumulative effect of individual component tolerances in an assembly. You can use the worst-case or statistical methods, such as Root Sum Square (RSS) or Monte Carlo simulation, depending on the complexity of the assembly and your requirements.
How do you calculate stack up analysis? To perform a tolerance stack-up analysis, you follow these steps:
- List all components and their respective tolerances.
- Determine the assembly sequence.
- Calculate the worst-case scenario by adding or subtracting the tolerances in the sequence.
- Evaluate if the result meets design requirements or if additional adjustments are needed.
What is the formula for calculating tolerance? The formula for calculating tolerance depends on the specific requirement. In general, you subtract the lower tolerance limit from the upper tolerance limit to determine the tolerance range. For example, Tolerance = Upper Limit – Lower Limit.
How do you calculate RSS for tolerances? To calculate the Root Sum Square (RSS) of tolerances, follow these steps:
- Square each individual tolerance value.
- Sum the squared values.
- Take the square root of the sum to obtain the RSS value.
How does a stack-based calculator work? A stack-based calculator uses a stack data structure to perform arithmetic operations. Numbers are pushed onto the stack, and operations are performed on the top elements of the stack. The result is then pushed back onto the stack. It uses a Last-In-First-Out (LIFO) approach for calculations.
How do you calculate clearance fit tolerance? Clearance fit tolerance is determined based on the desired clearance between mating parts. You subtract the minimum desired clearance from the maximum desired clearance to calculate the tolerance. For example, Tolerance = Maximum Clearance – Minimum Clearance.
What is the difference between GD&T and tolerance stack-up analysis? Geometric Dimensioning and Tolerancing (GD&T) is a system for specifying and controlling the form, orientation, location, and size of features on a part drawing. Tolerance stack-up analysis, on the other hand, is a method used to assess the cumulative impact of component tolerances in an assembly to ensure that the assembly functions correctly. GD&T provides the tolerances for individual features, while tolerance stack-up analysis considers how these tolerances add up in an assembly.
What is tolerance stack-up analysis with GD&T? Tolerance stack-up analysis with GD&T involves using geometric tolerances specified on a drawing to perform a stack-up analysis. This analysis helps determine whether the geometric tolerances for individual features will still allow the assembly to meet its functional requirements when assembled.
What is tolerance stack analysis in GD&T? Tolerance stack analysis in GD&T is the process of evaluating the cumulative effect of geometric tolerances on an assembly to ensure that the assembly will function within acceptable limits. It involves considering how the geometric tolerances of various features interact when assembled.
How do you calculate tolerance in Excel? You can calculate tolerance in Excel by subtracting the lower limit from the upper limit. For example, if the upper limit is in cell A1 and the lower limit is in cell A2, you can use the formula “=A1-A2” in another cell to calculate the tolerance.
How do you find the tolerance value in Excel? To find the tolerance value in Excel, simply subtract the lower limit from the upper limit using a formula, as mentioned above.
What are the three types of tolerance? The three primary types of tolerance are:
- Dimensional Tolerance: Specifies the allowable variation in the size of a feature.
- Geometric Tolerance: Specifies the allowable variation in form, orientation, and location of features using GD&T symbols.
- Positional Tolerance: A specific type of geometric tolerance that controls the location of a feature relative to a datum.
What is RSS in tolerance Stackup? RSS (Root Sum Square) in tolerance stack-up is a method used to calculate the combined effect of multiple tolerances in an assembly. It provides a conservative estimate of the overall tolerance by taking the square root of the sum of squared individual tolerances.
What is RSS calculation? The RSS calculation involves taking the square root of the sum of the squared values. It’s commonly used in tolerance stack-up analysis to determine the worst-case scenario for the combined effect of tolerances.
How do you calculate upper and lower tolerance? To calculate upper and lower tolerance limits, you add and subtract half of the tolerance range from the nominal value. For example, Upper Limit = Nominal Value + (Tolerance / 2), and Lower Limit = Nominal Value – (Tolerance / 2).
How do you calculate stacking percentage? Stacking percentage is typically used in the context of tolerance stack-up analysis. To calculate it, you can use the formula: Stacking Percentage = (Actual Stack-up Result / Allowable Stack-up Tolerance) x 100%.
How do you calculate stack size? Stack size refers to the cumulative effect of tolerances in a tolerance stack-up analysis. To calculate stack size, add up all the individual tolerances in the stack.
How do you use the stack method? The stack method is used in tolerance stack-up analysis to assess the cumulative impact of component tolerances in an assembly. You list the components, their tolerances, and their assembly sequence. Then, you calculate the worst-case or statistical outcomes to ensure the assembly meets design requirements.
What is the difference between clearance and tolerance? Clearance refers to the intentional gap or space between two mating parts in an assembly, allowing for relative movement. Tolerance, on the other hand, refers to the allowable variation in dimensions or other specifications of individual parts or features.
What three different types of tolerances might you find on a drawing? Three different types of tolerances you might find on a drawing are dimensional tolerances (size), geometric tolerances (form, orientation, location), and positional tolerances (location relative to a datum).
What is the standard tolerance size? The standard tolerance size varies depending on the specific engineering or manufacturing standards and the requirements of the design. There is no universal “standard” tolerance size; it depends on the application and industry standards.
What is the 3 2 1 rule in GD&T? The 3-2-1 rule in GD&T is a guideline used for locating features relative to a primary datum. It states that if three features are used to locate a part, at least two of them must contact the primary datum, and one must contact the secondary datum. This rule helps ensure proper alignment and control in geometric tolerancing.
What is the rule #1 and 2 in GD&T? Rule #1 in GD&T states that you must establish a datum before applying geometric tolerances. Rule #2 states that datums should be used in the order of their importance, with primary datums having the highest importance, followed by secondary and tertiary datums.
What are the two types of tolerance analysis? The two main types of tolerance analysis are:
- Worst-Case Tolerance Analysis: This method calculates the extreme values of the assembly by adding or subtracting tolerances linearly. It provides a conservative estimate of the assembly’s performance.
- Statistical Tolerance Analysis: This method uses statistical techniques like Monte Carlo simulation to analyze the variability of assembly results. It provides a more realistic assessment of performance.
What are the five main types of tolerances? The five main types of tolerances are:
- Dimensional Tolerance
- Geometric Tolerance
- Positional Tolerance
- Form Tolerance
- Profile Tolerance
What are the different types of tolerance stack-up analysis? Different types of tolerance stack-up analysis include worst-case analysis, RSS (Root Sum Square) analysis, statistical analysis (Monte Carlo simulation), and 1D tolerance stack-up analysis, among others.
What is maximum tolerance stacking? Maximum tolerance stacking refers to the worst-case scenario in a tolerance stack-up analysis, where all component tolerances add up in a way that maximizes the deviation from the nominal or desired result. It represents the most critical condition for the assembly.
How do you read a tolerance drawing? Reading a tolerance drawing involves interpreting the symbols and dimensions specified on the drawing. You’ll need to understand the GD&T symbols, dimensional tolerances, geometric tolerances, and any other annotations to determine the part’s design intent and manufacturing requirements.
How can you avoid tolerance stacking? To avoid tolerance stacking issues, you can:
- Design for larger tolerances where possible.
- Use geometric tolerancing and feature control frames to control part features.
- Utilize GD&T principles for proper feature control.
- Consider functional gauges or fixtures for critical mating parts.
- Use statistical analysis or computer-aided tolerance analysis tools.
What is the difference between tolerance and geometric tolerance? Tolerance is a general term referring to the allowable variation in dimensions, form, position, or other specifications of a part. Geometric tolerance, on the other hand, is a specific type of tolerance that controls the form, orientation, and location of features using GD&T symbols and principles.
How do you make a tolerance chart? To create a tolerance chart, list all the components in your assembly, along with their nominal values and tolerances. Then, calculate the worst-case stack-up for each component and the overall stack-up result. Display this information in a clear tabular format.
What is a tolerance chart? A tolerance chart is a visual representation or tabular summary of the tolerance stack-up analysis for an assembly. It shows the cumulative effect of component tolerances and helps ensure that the assembly meets design requirements.
What is the range of tolerance? The range of tolerance refers to the allowable variation between the upper and lower limits for a particular dimension or specification. It represents the acceptable deviation from the nominal value.
How do you write tolerance +- in Excel? You can write tolerance ± in Excel using the following characters: “±” or “ALT+0177” (hold the Alt key and type 0177 on the numeric keypad). These characters indicate a tolerance range with a plus-minus symbol.
What is the tolerance of a measured value? The tolerance of a measured value represents the acceptable deviation or variation from the nominal or target value. It defines the range within which the measured value should fall to meet design or quality standards.
Can Excel calculate RSD? Yes, Excel can calculate the Relative Standard Deviation (RSD). You can use the formula “=STDEVP(range)/AVERAGE(range)” for the population RSD or “=STDEV.S(range)/AVERAGE(range)” for the sample RSD, where “range” is the data range for which you want to calculate the RSD.
What is an example of tolerance measurement? An example of tolerance measurement is checking the diameter of a machined shaft. If the design specifies a diameter of 10.00 mm with a tolerance of ±0.02 mm, you would measure the shaft’s diameter and ensure that it falls within the range of 9.98 mm to 10.02 mm to meet the tolerance requirement.
What are the most common tolerances? The most common tolerances include dimensional tolerances (e.g., ±0.01 mm), positional tolerances (e.g., ±0.05 mm), and geometric tolerances (e.g., straightness of 0.02 mm).
What are the 6 types of tolerance? The six types of tolerance in engineering and manufacturing are:
- Dimensional Tolerance
- Geometric Tolerance
- Positional Tolerance
- Form Tolerance
- Profile Tolerance
- Runout Tolerance
What is worst-case tolerance stack-up? Worst-case tolerance stack-up analysis involves calculating the extreme or most unfavorable combination of component tolerances in an assembly. It ensures that even under the worst conditions, the assembly will meet its functional requirements.
What is CPK in tolerance analysis? CPK is a statistical measure used in tolerance analysis to assess the capability of a manufacturing process to produce parts within specified tolerances. It evaluates the process’s ability to stay within tolerance limits and is calculated as (USL – LSL) / (6σ), where USL is the upper specification limit, LSL is the lower specification limit, and σ is the process standard deviation.
What is 1D tolerance stack-up? 1D tolerance stack-up analysis is a simplified method of tolerance analysis that considers variations in a single direction or dimension. It’s often used for linear or one-dimensional assemblies.
How do you manually calculate RSS? To manually calculate the Root Sum Square (RSS) of multiple values, follow these steps:
- Square each value.
- Sum the squared values.
- Take the square root of the sum to obtain the RSS value.
What is a good RSS value? A good RSS value in tolerance stack-up analysis depends on the specific design and manufacturing requirements. Generally, a lower RSS value indicates tighter control and reduced variation. However, what constitutes a “good” value varies from one application to another.
What is RSS in GD&T? In GD&T (Geometric Dimensioning and Tolerancing), RSS is not a specific GD&T concept but rather a method used in tolerance stack-up analysis to calculate the cumulative effect of tolerances on an assembly. It stands for Root Sum Square and helps assess the worst-case scenario.
What does the tolerance of +/- 2% mean? A tolerance of +/- 2% means that a dimension or measurement can vary by up to 2% in either direction from the nominal or target value. For example, if the nominal value is 100 units, the acceptable range would be from 98 units to 102 units.
What is a 95% tolerance interval? A 95% tolerance interval is a statistical measure that provides a range within which a certain percentage (95% in this case) of data points or measurements are expected to fall. It is used to express confidence in the range of values for a given parameter.
What is the percentage stack chart? A percentage stack chart is a graphical representation used to visualize the contribution of individual components or factors to a total value. Each component is represented as a stacked segment, and the total height of the segments represents 100%. It helps illustrate the relative proportions of different factors.
What is percentage formula? The percentage formula is (Part / Whole) x 100%, where “Part” is the portion or value you want to express as a percentage of the “Whole.” It helps calculate the percentage of a value relative to a total.
What is the stacking ratio of material? The stacking ratio of material refers to the relationship between the height or volume of material in a stack and the available space or container volume. It is typically expressed as a ratio or percentage to assess how efficiently the space is utilized.
What is a stack calculator? A stack calculator is a type of electronic calculator that uses a stack-based data structure for performing calculations. It follows the Last-In-First-Out (LIFO) principle, where numbers and operations are pushed onto a stack, and results are obtained by popping items from the stack.
What is a stack-based calculator? A stack-based calculator is a calculator that uses a stack data structure to perform arithmetic operations. It stores numbers and operators in a stack, and calculations are performed on the top elements of the stack.
How does a stack calculator work? A stack calculator works by following a Last-In-First-Out (LIFO) approach for calculations. Numbers and operators are pushed onto a stack, and operations are performed on the top elements of the stack. The result is then pushed back onto the stack for further calculations.
What are the 3 primary methods for a stack? The three primary methods for a stack in computer science and calculators are:
- Push: Adding an item to the top of the stack.
- Pop: Removing and retrieving the top item from the stack.
- Peek: Viewing the top item of the stack without removing it.
What are the three stack methods? The three stack methods are:
- Push: Adding an item to the top of the stack.
- Pop: Removing and retrieving the top item from the stack.
- Peek: Viewing the top item of the stack without removing it.
What are stack methods? Stack methods are operations or functions used to manipulate a stack data structure. The primary stack methods include push (to add an item to the top of the stack), pop (to remove and retrieve the top item from the stack), and peek (to view the top item without removing it).
How many levels of tolerance are there? There can be multiple levels of tolerance in a manufacturing process, depending on the complexity of the product and the criticality of various features. Typically, there are primary tolerances for critical dimensions and secondary tolerances for less critical dimensions.
What does size tolerance mean? Size tolerance refers to the allowable variation in the dimensions of a part or feature. It specifies the acceptable range within which the actual size can deviate from the nominal or target size.
What are the three basic tolerances? The three basic tolerances are:
- Dimensional Tolerance: Controls the size of a feature.
- Geometric Tolerance: Controls the form, orientation, and location of features using GD&T symbols.
- Positional Tolerance: A specific type of geometric tolerance that controls the location of a feature relative to a datum.
How are tolerances measured? Tolerances are typically measured using various metrology tools and equipment such as calipers, micrometers, coordinate measuring machines (CMMs), and optical measuring systems. These tools allow for precise measurement of dimensions and features to ensure they meet the specified tolerances.
What are the 4 types of form tolerances? The four types of form tolerances in GD&T are:
- Straightness: Ensures that a line element is straight.
- Flatness: Ensures that a surface is flat without warping or waviness.
- Circularity: Ensures that a feature, like a hole or a cylinder, is circular in cross-section.
- Cylindricity: Ensures that a feature, like a cylinder, maintains a uniform diameter along its entire length.
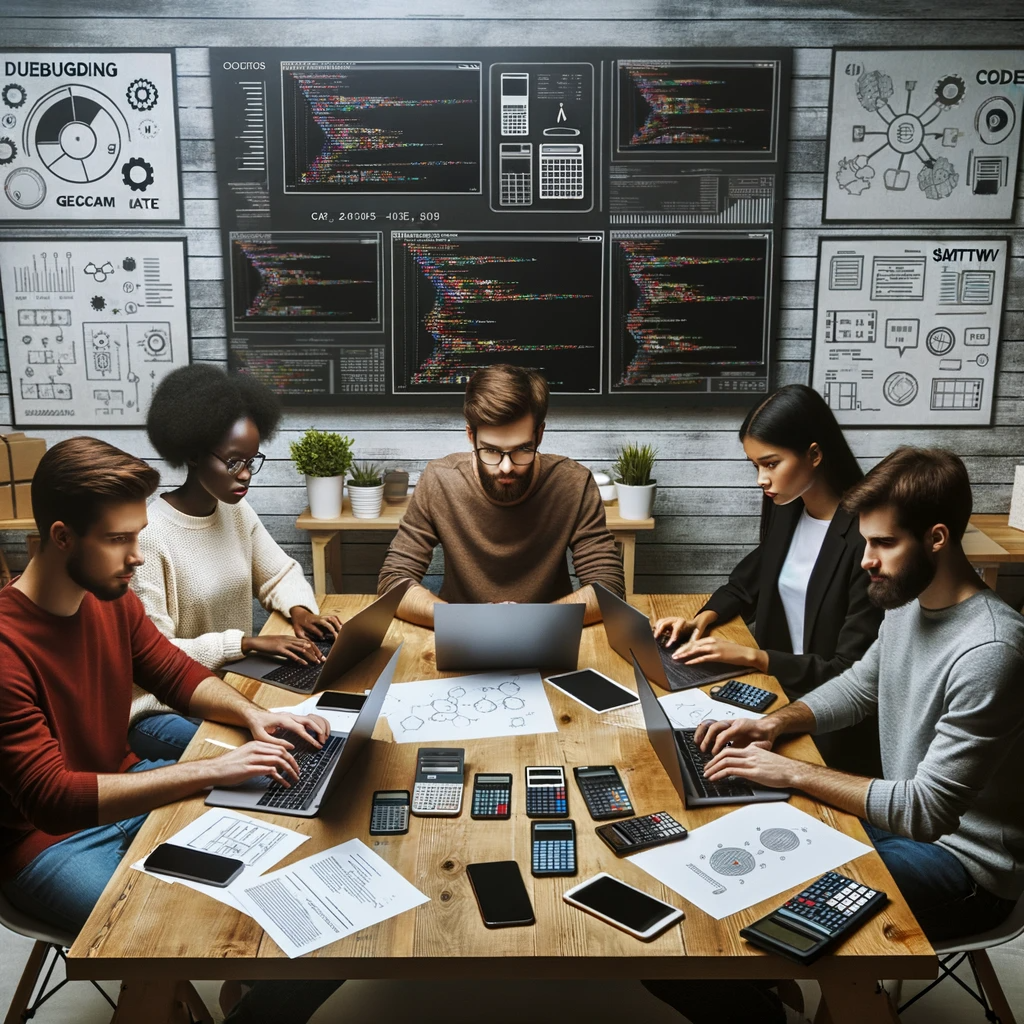
GEG Calculators is a comprehensive online platform that offers a wide range of calculators to cater to various needs. With over 300 calculators covering finance, health, science, mathematics, and more, GEG Calculators provides users with accurate and convenient tools for everyday calculations. The website’s user-friendly interface ensures easy navigation and accessibility, making it suitable for people from all walks of life. Whether it’s financial planning, health assessments, or educational purposes, GEG Calculators has a calculator to suit every requirement. With its reliable and up-to-date calculations, GEG Calculators has become a go-to resource for individuals, professionals, and students seeking quick and precise results for their calculations.