The torque of a hydraulic motor can vary widely depending on its design and specifications. It typically ranges from a few hundred to several thousand foot-pounds (ft-lbs) of torque.
Hydraulic Motor Torque Calculator
Parameter | Description | Units |
---|---|---|
Pressure (P) | The hydraulic pressure supplied to the motor. | Pascals (Pa) |
Flow Rate (Q) | The rate of hydraulic fluid flow into the motor. | Liters per minute (L/min) or Gallons per minute (GPM) |
Motor Efficiency (η) | The efficiency of the hydraulic motor. | Percentage (%) |
Displacement (V) | The motor displacement volume per rotation. | Cubic inches per revolution (in³/rev) or Milliliters per revolution (ml/rev) |
Torque (T) | The output torque generated by the motor. | Newton-meters (Nm) or Pound-feet (lb-ft) |
FAQs
How do you calculate the torque of a hydraulic motor? The torque of a hydraulic motor can be calculated using the formula: Torque (in ft-lbs) = Pressure (in psi) x Displacement (in cubic inches per revolution) / 6.28
What is the torque of a hydraulic motor? The torque of a hydraulic motor varies widely depending on its design and specifications. It can range from a few hundred ft-lbs to several thousand ft-lbs.
What is the maximum torque of a hydraulic motor? The maximum torque of a hydraulic motor depends on its design and specifications. It can vary significantly but is typically specified by the manufacturer in the motor’s technical documentation.
What is the torque ripple of a hydraulic motor? Torque ripple is a measure of the variation in torque output during one complete rotation of the hydraulic motor shaft. It is typically expressed as a percentage of the average torque.
How do you calculate torque of a motor in ft-lbs? Torque in ft-lbs can be calculated by multiplying the force (in pounds) applied perpendicular to a lever arm (in feet) from the rotational axis. The formula is: Torque (in ft-lbs) = Force (in lbs) x Lever Arm Length (in feet).
How do you calculate the torque power of a motor? Torque power is usually referred to as horsepower (HP). You can calculate horsepower using the formula: Horsepower (HP) = Torque (ft-lbs) x RPM / 5252.
How do you size a hydraulic motor? Sizing a hydraulic motor involves considering factors such as the required torque, speed, pressure, and flow rate for a specific application. Manufacturers often provide selection guides and software tools to assist in sizing hydraulic motors.
What does the torque of a hydraulic motor depend on? The torque of a hydraulic motor depends on factors like pressure, displacement, design efficiency, and the specific application requirements.
Why is starting torque important to determine when applying a hydraulic motor? Starting torque is important because it determines whether the hydraulic motor can overcome initial resistance and start moving the load. It’s crucial for applications that require overcoming static friction or inertia.
What is the formula for maximum torque of a motor? The formula for the maximum torque of a motor is specific to the motor’s design and can vary. It’s typically provided by the motor manufacturer in the motor’s technical documentation.
How do you match a hydraulic pump and motor? To match a hydraulic pump and motor, you need to consider their displacement, speed, and efficiency to ensure they can meet the hydraulic system’s requirements. It’s often done through hydraulic system design and calculation.
How do you size a hydraulic motor to a pump? Sizing a hydraulic motor to a pump involves matching their displacements and other specifications to ensure compatibility and achieve the desired output.
How much torque does a hydraulic pump need? The torque required by a hydraulic pump depends on the load it is driving and the system’s pressure and flow requirements. It can vary widely.
What is the difference between cogging torque and torque ripple? Cogging torque is a phenomenon in electric motors where there is a periodic variation in torque due to magnetic interactions. Torque ripple, as mentioned earlier, is the variation in torque output during one rotation of a hydraulic motor shaft.
What is the available torque delivered by a hydraulic motor with a pressure of 3200 psi and a displacement of 2.146 cu in? Using the torque formula mentioned earlier: Torque (ft-lbs) = Pressure (psi) x Displacement (cubic inches per revolution) / 6.28, we can estimate the torque. Torque = 3200 psi x 2.146 cu in / 6.28 ≈ 1083 ft-lbs
How do you calculate hydraulic torque? Hydraulic torque can be calculated using the formula mentioned earlier: Torque (ft-lbs) = Pressure (psi) x Displacement (cubic inches per revolution) / 6.28.
How many inch-pounds does it take to make 1 lb of torque? There are 12 inch-pounds (in-lbs) in 1 foot-pound (ft-lb), so it takes 12 in-lbs to make 1 lb of torque.
How do I calculate how much torque I need? Calculating the required torque depends on your specific application. You’ll need to consider factors like the load, distance from the axis of rotation, and any friction or resistance.
What is the torque of a motor? The torque of a motor varies depending on the motor’s design and specifications. It is typically specified by the motor manufacturer.
What is the torque constant of a motor? The torque constant (Kt) of a motor is a parameter that relates the motor’s torque output to the current passing through it. It is usually given in units of Nm/A (Newton meters per ampere) for electric motors.
How do you calculate motor power from RPM and torque? Motor power (in watts) can be calculated as the product of torque (in Nm) and angular velocity (in radians per second), which can be converted from RPM. The formula is: Power (W) = Torque (Nm) x Angular Velocity (radians/second).
What is the strongest hydraulic motor? The strength of a hydraulic motor depends on various factors, including its size, design, and intended application. “Strongest” can vary widely depending on specific requirements.
How much horsepower do you need to run a hydraulic pump? The horsepower required to run a hydraulic pump depends on the pump’s flow rate, pressure, and efficiency, as well as the specific application.
How do you calculate the horsepower of a hydraulic motor? Horsepower for a hydraulic motor can be calculated using the formula: Horsepower (HP) = Torque (ft-lbs) x RPM / 5252.
How does hydraulic torque work? Hydraulic torque is generated by the pressure difference across the motor’s pistons, causing them to move and turn the motor’s shaft. This converts hydraulic energy into mechanical torque.
Should a hydraulic motor spin freely? Hydraulic motors should not spin freely when pressurized fluid is applied. They should provide torque and power to drive a load.
Does motor torque depend on voltage? The torque produced by an electric motor depends on the current flowing through it, which is related to voltage and the motor’s design. However, it’s not solely determined by voltage.
When large amounts of starting torque are needed, the best motor is? When large starting torque is needed, a motor with a high torque-to-inertia ratio is ideal. This might be a high-torque electric motor or a hydraulic motor, depending on the application.
Why is high starting torque good? High starting torque is good because it allows a motor to overcome resistance and initiate motion more easily, reducing the risk of stalling or overloading.
Does starting torque higher than full load torque? Yes, starting torque is typically higher than the full load torque for most motors because it needs to overcome initial resistance and inertia.
What is the formula for starting torque and maximum torque? The formula for starting torque and maximum torque depends on the motor’s design and specifications, so there is no single formula that applies universally.
What is 9.5488 in torque calculation? 9.5488 is an approximate conversion factor used to convert from watts (W) to horsepower (HP) when calculating motor power. It is commonly used because 1 HP is approximately equal to 746 watts.
Can a hydraulic motor turn both ways? Yes, hydraulic motors can typically be designed to turn in both clockwise and counterclockwise directions by changing the direction of fluid flow.
What is the pressure in a hydraulic motor? The pressure in a hydraulic motor depends on the hydraulic system’s design and operating conditions. Common pressures can range from hundreds to thousands of psi.
How do I know if my hydraulic pump motor is bad? Signs of a bad hydraulic pump or motor may include decreased performance, unusual noises, fluid leaks, or excessive heat. It’s best to consult a professional for diagnosis and repair.
What happens if your hydraulic pump is too big? If a hydraulic pump is oversized for an application, it may cause inefficiency and potentially lead to excessive pressure and heat in the system. It can also waste energy.
Is a hydraulic motor the same as a hydraulic pump? No, a hydraulic motor and a hydraulic pump are not the same. A hydraulic pump is used to generate hydraulic fluid flow, while a hydraulic motor converts hydraulic fluid flow into mechanical motion.
What is the formula for a hydraulic pump? There isn’t a single formula for a hydraulic pump, as pump design and specifications vary widely. Hydraulic pump selection involves considering factors like flow rate, pressure, and displacement.
What is the torque efficiency of a hydraulic motor? Torque efficiency refers to the ability of a hydraulic motor to convert hydraulic power into mechanical torque efficiently. It depends on the motor’s design and efficiency.
How do you calculate the force of a hydraulic pump? The force generated by a hydraulic pump depends on the pressure it produces and the area over which the pressure acts (usually a piston or cylinder). The formula is: Force (in pounds) = Pressure (in psi) x Area (in square inches).
Why is cogging torque bad? Cogging torque in electric motors causes unwanted variation in torque, resulting in vibration and noise, which can be detrimental to precision and smooth operation.
What are the disadvantages of cogging torque? The disadvantages of cogging torque include decreased motor efficiency, increased wear and tear, and reduced accuracy in applications requiring smooth and precise motion.
What is the problem with cogging torque? The problem with cogging torque is that it creates undesired fluctuations in torque output, leading to uneven motion and potential issues in applications requiring consistent and smooth movement.
At what PSI do most hydraulic systems operate at? Many hydraulic systems operate in the range of 1,000 to 3,000 psi (pounds per square inch), but the operating pressure can vary depending on the application.
What is the formula for torque displacement of a hydraulic motor? The formula for torque displacement of a hydraulic motor is Torque (ft-lbs) = Pressure (psi) x Displacement (cubic inches per revolution) / 6.28, as mentioned earlier.
How do you match a hydraulic pump to a motor? Matching a hydraulic pump to a motor involves ensuring that the pump’s flow rate and pressure capabilities are compatible with the motor’s displacement and torque requirements.
How much weight can a 3200 psi hydraulic pump lift? The weight that a hydraulic pump can lift depends on various factors, including the pump’s flow rate, pressure, and the mechanical advantage of the hydraulic system. It can vary widely.
How do I size a hydraulic motor? Sizing a hydraulic motor involves considering factors like the required torque, speed, pressure, and flow rate for a specific application. Manufacturers often provide selection guides and software tools to assist in sizing hydraulic motors.
How much torque is 100 inch-pounds? 100 inch-pounds of torque is equivalent to 8.33 foot-pounds (ft-lbs) of torque.
How much torque is 50 inch-pounds? 50 inch-pounds of torque is equivalent to 4.17 foot-pounds (ft-lbs) of torque.
How much is 5 ft-lbs of torque? 5 foot-pounds (ft-lbs) of torque is equivalent to 60 inch-pounds of torque.
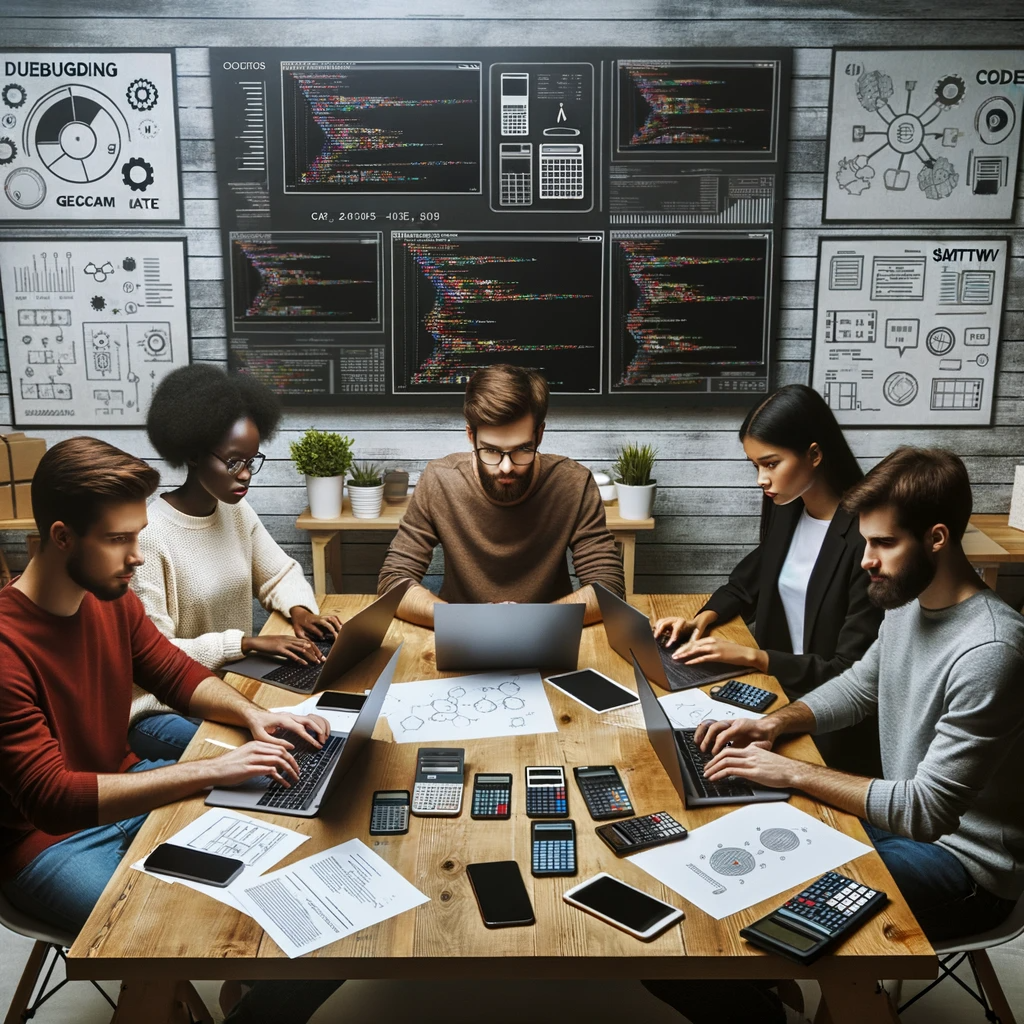
GEG Calculators is a comprehensive online platform that offers a wide range of calculators to cater to various needs. With over 300 calculators covering finance, health, science, mathematics, and more, GEG Calculators provides users with accurate and convenient tools for everyday calculations. The website’s user-friendly interface ensures easy navigation and accessibility, making it suitable for people from all walks of life. Whether it’s financial planning, health assessments, or educational purposes, GEG Calculators has a calculator to suit every requirement. With its reliable and up-to-date calculations, GEG Calculators has become a go-to resource for individuals, professionals, and students seeking quick and precise results for their calculations.