Injection molding cooling time varies depending on factors like material, part design, and mold configuration. Typically, it ranges from a few seconds to several minutes per cycle. Precise calculation involves material-specific heat transfer rates and mold geometry, making it challenging to provide a specific time without detailed information.
Injection Molding Cooling Time Calculator
Plastic Material | Approximate Cooling Time (seconds per cycle) |
---|---|
ABS | 10-30 |
Polypropylene (PP) | 15-45 |
Polystyrene (PS) | 10-30 |
Polycarbonate (PC) | 20-60 |
Acrylic (PMMA) | 15-45 |
Nylon (PA) | 20-50 |
Polyethylene (PE) | 10-30 |
FAQs
How do you calculate cooling time in injection molding? Cooling time in injection molding can be estimated using the following formula: Cooling Time (in seconds) ≈ (T1 – T2) / Cooling Rate
What is the formula for mould cooling? There isn’t a single formula for mold cooling, as it depends on various factors including material, part geometry, mold design, and cooling system efficiency. Generally, it involves calculating the required heat transfer rate and determining the cooling system’s capacity to meet that rate.
What is the cooling rate in injection molding? The cooling rate can vary widely but is typically in the range of 5-30°C (9-54°F) per second.
How can cooling time be reduced in injection molding? Cooling time can be reduced by improving the mold design, using efficient cooling channels, optimizing the cooling system, and using materials with better thermal properties.
What is the formula for cooling time? Cooling Time (in seconds) ≈ (T1 – T2) / Cooling Rate
How do you calculate cooling hours? Cooling Hours = Cooling Time (in seconds) / 3,600 (to convert seconds to hours)
When cooling a mold, which method of cooling is best? The best cooling method depends on the specific requirements of the injection molding process. Common methods include water cooling, oil cooling, and air cooling. Water cooling is often preferred due to its efficiency.
How is cooling done in injection molding? Cooling is typically achieved by circulating a cooling medium (usually water) through channels in the mold. The heated plastic part transfers its heat to the mold, and the cooling medium removes that heat.
How do you calculate chiller capacity for injection molding? Chiller capacity depends on the heat load of the injection molding process. A rough estimation can be made by calculating the total energy required to cool the plastic, which includes the material’s heat capacity, mass, and cooling time.
Does cooling rate affect shrinkage? Yes, the cooling rate can affect the shrinkage of plastic parts. Faster cooling can lead to higher levels of residual stress and may result in greater shrinkage.
What is the rate of cooling? The rate of cooling is the speed at which an object or material loses heat, typically measured in degrees Celsius (or Fahrenheit) per unit of time (e.g., degrees Celsius per second).
What is critical rate of cooling? The critical rate of cooling is the minimum cooling rate required to prevent the formation of certain undesirable microstructures in materials during cooling processes, such as in heat treatment.
How do you control cooling rate? Cooling rate can be controlled by adjusting the temperature of the cooling medium, the design of the cooling channels in the mold, and the flow rate of the cooling medium.
How long does plastic take to cool? The cooling time for plastic parts in injection molding can range from a few seconds to several minutes, depending on the material, part geometry, and other factors.
What is the typical cycle time for injection molding? Cycle times for injection molding can vary widely but typically range from 10 seconds to a few minutes.
What is the total cooling time? Total cooling time is the time it takes for a plastic part to cool from its molten state to a temperature where it can be safely ejected from the mold.
What is cooling time constant? The cooling time constant is a parameter used in heat transfer calculations and represents the time it takes for a material or object to cool down to a certain percentage of its initial temperature.
What is cooling cycles per hour? Cooling cycles per hour refer to the number of complete cooling cycles a molding machine can perform in an hour.
How do you calculate temperature change time? Temperature Change Time = (T1 – T2) / Cooling Rate
How do you calculate temperature change per hour? Temperature Change Per Hour = (T1 – T2) / Total Cooling Time (in hours)
What is the quickest method of cooling? The quickest method of cooling depends on the application but generally involves using high-speed cooling systems and efficient heat transfer methods.
What is the 2 4 cooling method? The 2-4 cooling method is a rule of thumb in injection molding, suggesting that a part should cool for at least 2 seconds (2) before any motion of the mold and then an additional 4 seconds (4) before ejection.
What are 4 cooling methods? Common cooling methods include air cooling, water cooling, oil cooling, and forced convection cooling.
Why is cooling necessary for injection molding? Cooling is necessary in injection molding to solidify and cool down the molten plastic, allowing it to take on the desired shape and preventing distortion or warping of the part.
What temperature do you heat injection molding? Injection molding typically involves heating the plastic material to temperatures ranging from 200°C to 300°C (392°F to 572°F), depending on the material.
What is the typical temperature of injection mold? The typical mold temperature for injection molding is usually maintained between 20°C to 80°C (68°F to 176°F), depending on the material and part requirements.
How do you manually calculate chiller capacity for a process? Chiller capacity can be manually calculated by estimating the heat load of the process and the required temperature difference (ΔT). The formula is: Chiller Capacity (in kW) = Heat Load (in kW) / ΔT
How do you calculate cooling load? Cooling load is calculated by determining the heat gain or heat removal required to maintain a desired temperature. The formula is: Cooling Load (in kW) = Mass Flow Rate (in kg/s) × Specific Heat Capacity (in J/kg·K) × Temperature Difference (in K)
What is the formula for chiller flow rate? Chiller Flow Rate (in L/min) = Cooling Load (in kW) / (Density (in kg/L) × Specific Heat Capacity (in J/kg·K) × Temperature Difference (in K))
What is the cooling method? Cooling methods include various techniques for removing heat from a system or process, such as conduction, convection, and radiation, as well as specific methods like air cooling, water cooling, and refrigeration.
Why are injection molding dies water cooled? Injection molding dies are water cooled because water is an efficient heat transfer medium. Water-cooling channels in the mold help dissipate the heat generated during the injection molding process, ensuring proper cooling of the plastic material.
What is Delta T in chiller? Delta T (ΔT) in chiller systems refers to the temperature difference between the cooling medium (e.g., water) entering and exiting the chiller unit. It indicates the effectiveness of the cooling process.
What is cooling capacity in kW? Cooling capacity in kW represents the amount of heat energy a cooling system (e.g., chiller) can remove from a process or environment per unit of time, typically measured in kilowatts.
What is the minimum volume for a chiller? The minimum volume for a chiller depends on various factors, including the desired cooling capacity, temperature requirements, and the specific application. There is no fixed minimum volume.
Does volume affect rate of cooling? Yes, volume can affect the rate of cooling. A larger volume typically requires more time to cool compared to a smaller volume, assuming the same cooling capacity.
What temperature causes shrinkage? The temperature at which a material begins to shrink depends on the material itself. For many plastics, shrinkage begins at temperatures below their melting point.
Why does rate of cooling slow down? The rate of cooling may slow down due to factors like reduced temperature difference (ΔT) between the object and the cooling medium, reduced heat transfer surface area, or inadequate cooling capacity.
What factors affect cooling rate? Factors affecting cooling rate include cooling medium properties, temperature difference (ΔT), heat transfer surface area, material properties, and the efficiency of the cooling system.
What does the rate of cooling depend on? The rate of cooling depends on the factors mentioned earlier, including temperature difference, heat transfer, and material properties.
What is high cooling rate? A high cooling rate refers to a rapid rate at which an object or material loses heat, typically measured in degrees Celsius (or Fahrenheit) per unit of time.
Why is cooling rate important? Cooling rate is important because it affects the properties and quality of the final product. It can influence material properties, part dimensions, and overall manufacturing efficiency.
What does a higher cooling rate lead to? A higher cooling rate can lead to shorter cycle times, reduced energy consumption, and improved part quality in some cases. However, it may also result in increased residual stresses and potential for warping or cracking.
Why is the rate of cooling faster at the start? The rate of cooling is often faster at the start because the temperature difference (ΔT) between the hot object and the cooling medium is greater initially.
What is the best setting for cooling? The best setting for cooling depends on the specific process and material requirements. It often requires optimization through experimentation and process engineering.
What are the three cooling methods? Three common cooling methods are air cooling, water cooling, and oil cooling. Each has its own advantages and is suitable for different applications.
How hot is too hot for plastic? The temperature at which plastic becomes too hot varies by the type of plastic. Generally, temperatures near or above the material’s melting point are considered too hot for most plastics.
What happens when plastic gets too hot? When plastic gets too hot, it can melt, deform, lose its structural integrity, or release toxic fumes, depending on the type of plastic.
What cools faster, plastic or metal? Metal typically cools faster than plastic because metals have higher thermal conductivity, allowing heat to dissipate more rapidly.
How do you calculate injection cycle time? Injection cycle time is the sum of various time components such as injection time, cooling time, and ejection time. The formula is: Cycle Time = Injection Time + Cooling Time + Ejection Time
What are the 4 stages of injection molding? The four stages of injection molding are:
- Injection: Material is injected into the mold cavity.
- Cooling: The part cools and solidifies.
- Packing and Holding: Additional material is packed into the mold to compensate for shrinkage.
- Ejection: The finished part is ejected from the mold.
What is the minimum daylight in injection molding? The minimum daylight in injection molding refers to the minimum distance between the two halves of the mold when the mold is closed. It depends on the specific mold and machine design.
What is the 90-minute cooling rule? The 90-minute cooling rule is a guideline suggesting that plastic parts should cool for at least 90 minutes before being removed from the mold to avoid warping or distortion.
What is the 2-hour cooling rule? The 2-hour cooling rule is a similar guideline, suggesting that plastic parts should cool for at least 2 hours before removal.
How do you calculate cooling hours? Cooling Hours = Cooling Time (in hours) × Number of Cooling Cycles
What is the cooling time law? The cooling time law is a concept in heat transfer that describes how the temperature of an object changes over time as it cools down. It is typically described using exponential decay equations.
How do you calculate cooling days? Cooling Days are typically calculated based on the number of hours in a day when the temperature exceeds a certain threshold, often used for building energy analysis and HVAC system sizing.
Why is 63.2 a time constant? In exponential decay, a time constant of 63.2% (1 – 1/e) is used as a measure of how quickly a process reaches a steady-state or equilibrium condition.
What is a good cooling schedule? A good cooling schedule depends on the specific application and material. It involves optimizing cooling time, temperature, and pressure to achieve the desired part quality.
What is the rate of cooling explained? The rate of cooling is the rate at which an object’s temperature decreases over time due to heat loss to the surrounding environment. It is a measure of how quickly an object cools down.
What is the time constant of temperature change? The time constant of temperature change (τ) represents the time it takes for an object’s temperature to change by a certain fraction, often 63.2%, during a cooling or heating process.
What is the temperature change rule? The temperature change rule refers to how an object’s temperature changes over time due to heat transfer with its surroundings. It is often described by exponential decay equations.
What is the equation for time and temperature? The equation for time and temperature in a cooling or heating process can be described using exponential decay or growth equations, such as: T(t) = T0 + (T_initial – T0) * e^(-t/τ)
What is the formula for temperature conversion? Temperature conversion formulas allow you to convert temperature from one scale (e.g., Celsius) to another (e.g., Fahrenheit) and depend on the specific scales being converted.
What is the formula to calculate hour? There is no single formula to calculate hours, as it depends on what you are trying to find. Hours are typically calculated based on time intervals, and there are various formulas for specific calculations.
How do you calculate the rate of change per minute? The rate of change per minute can be calculated by dividing the change in a quantity (e.g., temperature) by the change in time (e.g., minutes). The formula is: Rate of Change per Minute = (Change in Quantity) / (Change in Time)
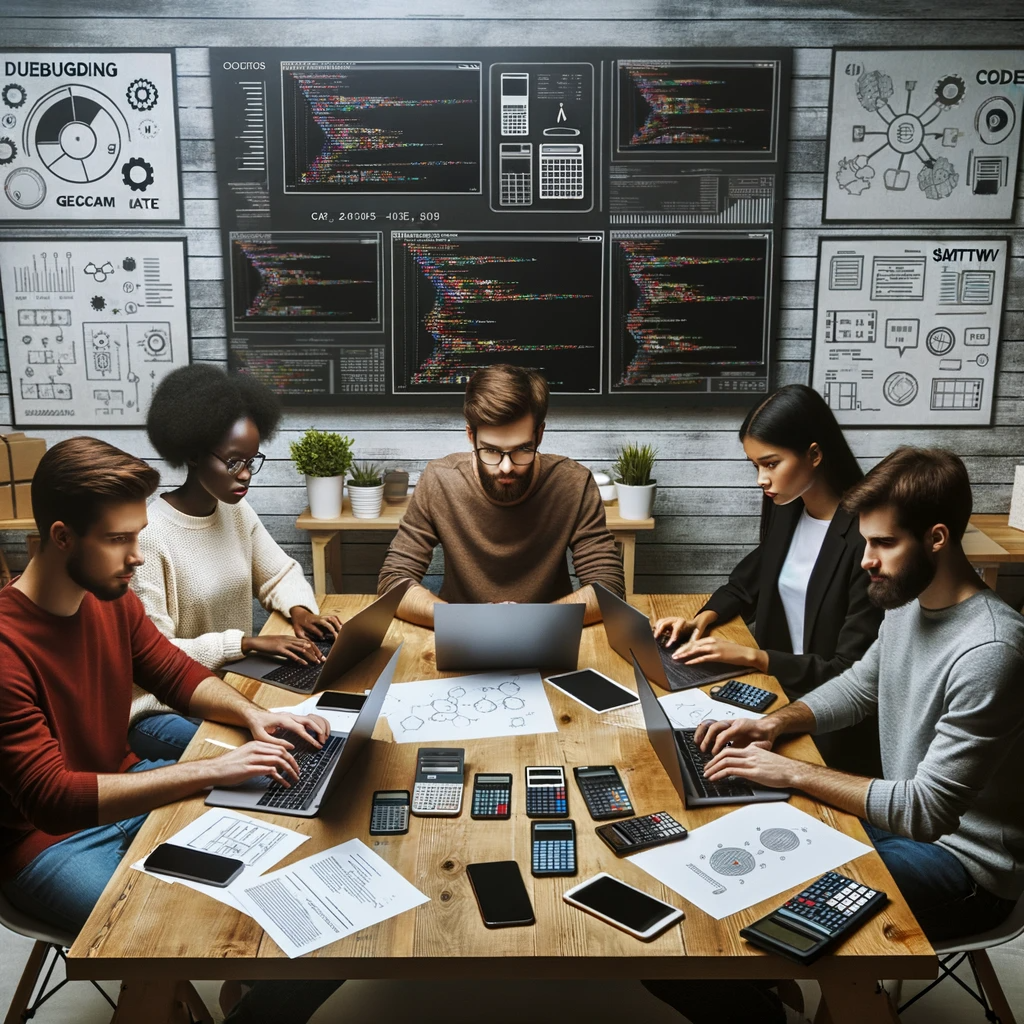
GEG Calculators is a comprehensive online platform that offers a wide range of calculators to cater to various needs. With over 300 calculators covering finance, health, science, mathematics, and more, GEG Calculators provides users with accurate and convenient tools for everyday calculations. The website’s user-friendly interface ensures easy navigation and accessibility, making it suitable for people from all walks of life. Whether it’s financial planning, health assessments, or educational purposes, GEG Calculators has a calculator to suit every requirement. With its reliable and up-to-date calculations, GEG Calculators has become a go-to resource for individuals, professionals, and students seeking quick and precise results for their calculations.