Thermoforming costs can range from $0.25 to $5 per part, depending on factors such as material choice, part complexity, production volume, and labor expenses. Material costs typically range from $0.25 to $3 per pound, while labor costs are approximately $15 to $30 per hour. Tooling costs for molds can vary widely, ranging from $1,000 to $10,000 per mold. Overhead expenses typically account for 20-30% of the total production cost.
Thermoforming Cost Calculator
Cost Component | Estimation Range |
---|---|
Material Cost | $0.25 – $3 per pound |
Labor Cost | $15 – $30 per hour |
Tooling Costs | $1,000 – $10,000 per mold |
Overhead Expenses | 20-30% of total production cost |
Total Production Cost | Varies widely based on part complexity, volume, and materials |
Cost per Part | $0.25 – $5 per part (for medium to large production runs) |
FAQs
How much does thermoforming cost? The cost of thermoforming can vary widely depending on factors like material choice, part complexity, production volume, and labor costs. As a rough estimate, thermoforming costs can range from $0.25 to $5 per part, with higher volumes generally reducing the cost per part.
How do you calculate the part cost? Part cost in thermoforming typically includes material cost, labor cost, tooling costs (if applicable), and overhead expenses. The formula to calculate part cost is:
Part Cost = Material Cost + Labor Cost + Tooling Costs + Overhead Expenses
Is thermoforming plastic expensive? Thermoforming plastic can vary in cost depending on the type of plastic used. Some thermoforming plastics can be relatively inexpensive, while others with specialized properties may be more costly. In general, thermoforming is often considered a cost-effective manufacturing process for producing plastic parts.
Is thermoforming cheap? Thermoforming is generally considered a cost-effective manufacturing process, especially for medium to large production volumes. It can be more cost-efficient than processes like injection molding for certain applications, but cost-effectiveness depends on factors like volume, part complexity, and material choice.
What is part of labor cost? Labor cost in thermoforming includes wages for operators and technicians involved in the production process. It also includes benefits, training, and any other labor-related expenses.
How do you calculate your total cost for production? Total production cost includes material costs, labor costs, tooling costs, overhead expenses, and any other production-related expenses. The formula to calculate total production cost is:
Total Production Cost = Material Cost + Labor Cost + Tooling Costs + Overhead Expenses + Other Production Expenses
What is cost per part? Cost per part is the cost associated with producing one unit of a particular product or component. It is calculated by dividing the total production cost by the number of parts produced.
Cost per Part = Total Production Cost / Number of Parts Produced
What are the cons of thermoforming? Some potential disadvantages of thermoforming include limited part design flexibility compared to injection molding, longer production times for complex parts, and limited suitability for high-precision applications. Additionally, it may not be ideal for very low-volume production runs.
What is the best plastic to thermoform? The best plastic for thermoforming depends on the specific requirements of the part, but some commonly used thermoforming plastics include ABS, PVC, PETG, and polycarbonate. The choice of material should consider factors like durability, appearance, and cost.
What is the easiest plastic to thermoform? Among commonly used plastics, PVC is often considered one of the easiest to thermoform due to its low melting point and good formability.
How long does thermoforming take? Thermoforming cycle times can vary widely depending on part complexity and equipment used. Generally, it can take anywhere from a few seconds to several minutes per part.
How thick can you thermoform? Thermoforming can be done with a wide range of plastic thicknesses, typically from 0.005 inches (0.127 mm) to 0.5 inches (12.7 mm) or more, depending on the equipment and material.
What is the minimum thickness for thermoforming? The minimum thickness for thermoforming largely depends on the material and the specific part design. However, thermoforming is often most efficient with materials that are at least 0.020 inches (0.5 mm) thick.
How to calculate labor costs? Labor costs are calculated by multiplying the number of labor hours worked by the hourly wage or labor rate. The formula for labor cost is:
Labor Cost = Number of Labor Hours × Hourly Wage or Labor Rate
What is a good labor cost percentage? A good labor cost percentage can vary by industry and company, but it’s generally considered favorable if labor costs account for around 20-35% of total production costs.
What is Labour hour rate? Labor hour rate (LHR) is the cost incurred per hour of labor. It includes wages, benefits, and other labor-related expenses. The formula for LHR is:
LHR = Total Labor Cost / Total Labor Hours
What is the formula for raw materials cost? The formula for raw materials cost is straightforward:
Raw Materials Cost = Quantity of Material Used × Cost per Unit of Material
What is the actual cost of production? The actual cost of production is the total cost incurred during the manufacturing process, including material costs, labor costs, overhead, and any other expenses directly related to production.
What is the full production cost? The full production cost includes all costs associated with producing a product, including material costs, labor costs, overhead expenses, tooling costs, and any other relevant expenses.
What is part of manufacturing cost? Manufacturing costs include all expenses associated with the production process, such as raw materials, labor, machinery, equipment maintenance, and factory overhead.
What are the three parts of cost? The three main components of cost in manufacturing are:
- Material Costs: The cost of raw materials or components used in production.
- Labor Costs: The cost of labor, including wages, benefits, and other labor-related expenses.
- Overhead Costs: The indirect costs of production, such as rent, utilities, equipment maintenance, and administrative expenses.
What is the most common thermoforming material? The most common thermoforming materials include ABS (Acrylonitrile Butadiene Styrene), PVC (Polyvinyl Chloride), and PETG (Polyethylene Terephthalate Glycol).
Is thermoforming cheaper than injection molding? Thermoforming is often more cost-effective than injection molding for medium to large production runs and for certain part geometries. However, for very high-volume production and intricate part designs, injection molding can be more cost-effective.
What is the future of thermoforming? The future of thermoforming may involve advancements in materials, automation, and sustainability. There may be increased use of recycled and biodegradable materials in thermoforming, as well as improved energy efficiency and process automation.
Is PVC better than PET for thermoforming? The choice between PVC and PET for thermoforming depends on the specific application. PVC is known for its ease of thermoforming and low cost, while PET offers clarity, toughness, and better resistance to some chemicals. The choice should consider the desired properties of the finished product.
Is thermoforming better than injection molding? Thermoforming and injection molding are suited to different applications. Thermoforming is better for low to medium production volumes and simpler part geometries, while injection molding excels in high-volume production and complex parts with tight tolerances.
Can you thermoform plexiglass? Yes, plexiglass (acrylic) can be thermoformed, but it requires precise temperature control and careful handling due to its sensitivity to heat. Thermoforming acrylic can produce clear and visually appealing parts.
What are the two most common types of thermoforming? The two most common types of thermoforming are vacuum forming and pressure forming. Vacuum forming uses a vacuum to shape the plastic over a mold, while pressure forming adds additional pressure to achieve more intricate details.
What is the thickest plastic you can vacuum form? The thickest plastic that can be vacuum formed depends on various factors, including the type of plastic, the equipment used, and the specific application. Generally, vacuum forming is most commonly used with plastic sheets ranging from 0.020 to 0.500 inches (0.5 to 12.7 mm) thick.
How thick is thermoforming plastic sheet? Thermoforming plastic sheets can range in thickness from as thin as 0.005 inches (0.127 mm) to 0.500 inches (12.7 mm) or more, depending on the material and application.
What is the 10 10 5 rule for thermoforming? The 10-10-5 rule in thermoforming refers to a guideline for designing undercuts in thermoformed parts. It suggests that undercuts should be no greater than 10% of the part depth, with 10 degrees of draft angle, and a minimum spacing of 5 times the material thickness between undercuts to facilitate easy part removal from the mold.
How big is the thermoforming market? The size of the thermoforming market can vary by region and industry. As of my last knowledge update in September 2021, the global thermoforming market was estimated to be worth billions of dollars, with growth expected in various sectors, including packaging, automotive, and electronics.
How hot is thermoforming? The temperature used in thermoforming can vary based on the type of plastic and the equipment. Typically, the plastic sheet is heated to a range of 300 to 400 degrees Fahrenheit (150 to 200 degrees Celsius) before forming.
Can thermoforming plastic be reheated? Thermoforming plastic can be reheated to a certain extent, but excessive reheating can lead to degradation of the material’s properties. It’s generally best to avoid multiple heating and cooling cycles whenever possible.
Is thermoformed plastic durable? The durability of thermoformed plastic depends on the material chosen, the thickness of the plastic, and the intended application. Thermoformed parts can be durable and long-lasting for many applications, but some may be less durable than injection-molded counterparts.
How accurate is thermoforming? Thermoforming can achieve good accuracy and repeatability for many parts, but it may not be as precise as processes like injection molding for achieving tight tolerances. The accuracy of thermoforming depends on factors like material, equipment, and tooling.
What material is mold for thermoforming? Thermoforming molds are typically made from materials like aluminum, steel, or composite materials. The choice of mold material depends on factors such as the production volume and the specific requirements of the part.
Does thermoforming use a vacuum? Yes, vacuum forming is a common type of thermoforming that uses a vacuum to draw heated plastic material over a mold to create the desired shape.
What are the basics of thermoforming? The basics of thermoforming involve heating a plastic sheet until it becomes pliable, positioning it over a mold, and using vacuum or pressure to shape the plastic into the desired form. It’s a widely used manufacturing process for producing various plastic parts and packaging.
How do you calculate labor cost and material cost? Labor cost is calculated by multiplying the number of labor hours by the hourly wage or labor rate. Material cost is calculated by multiplying the quantity of material used by the cost per unit of material. These costs are then added together to determine the total production cost.
What is the average labor vs. material cost? The average labor vs. material cost can vary widely by industry and company. In general, labor costs tend to be higher in labor-intensive industries, while material costs are more significant in material-intensive industries.
Why is my labor cost so high? Several factors can contribute to high labor costs, including high wages, inefficient processes, excessive overtime, and labor-intensive production methods. Identifying the specific reasons for high labor costs is essential to address the issue effectively.
What is high labor cost? High labor cost refers to a situation where a significant portion of the total production cost is attributed to labor expenses. This can impact the profitability and competitiveness of a business, especially if not properly managed.
How do you calculate labor cost in manufacturing? Labor cost in manufacturing is calculated by multiplying the number of labor hours worked by the hourly wage or labor rate. This cost may also include additional labor-related expenses such as benefits and training costs.
How do you calculate manufacturing hourly rate? Manufacturing hourly rate is calculated by dividing the total labor cost for a specific period (e.g., a month) by the total number of labor hours worked during that period.
What is an example of a labor cost? An example of a labor cost is the hourly wage of a production worker. Other labor costs may include overtime pay, benefits such as health insurance or retirement contributions, and training expenses for employees.
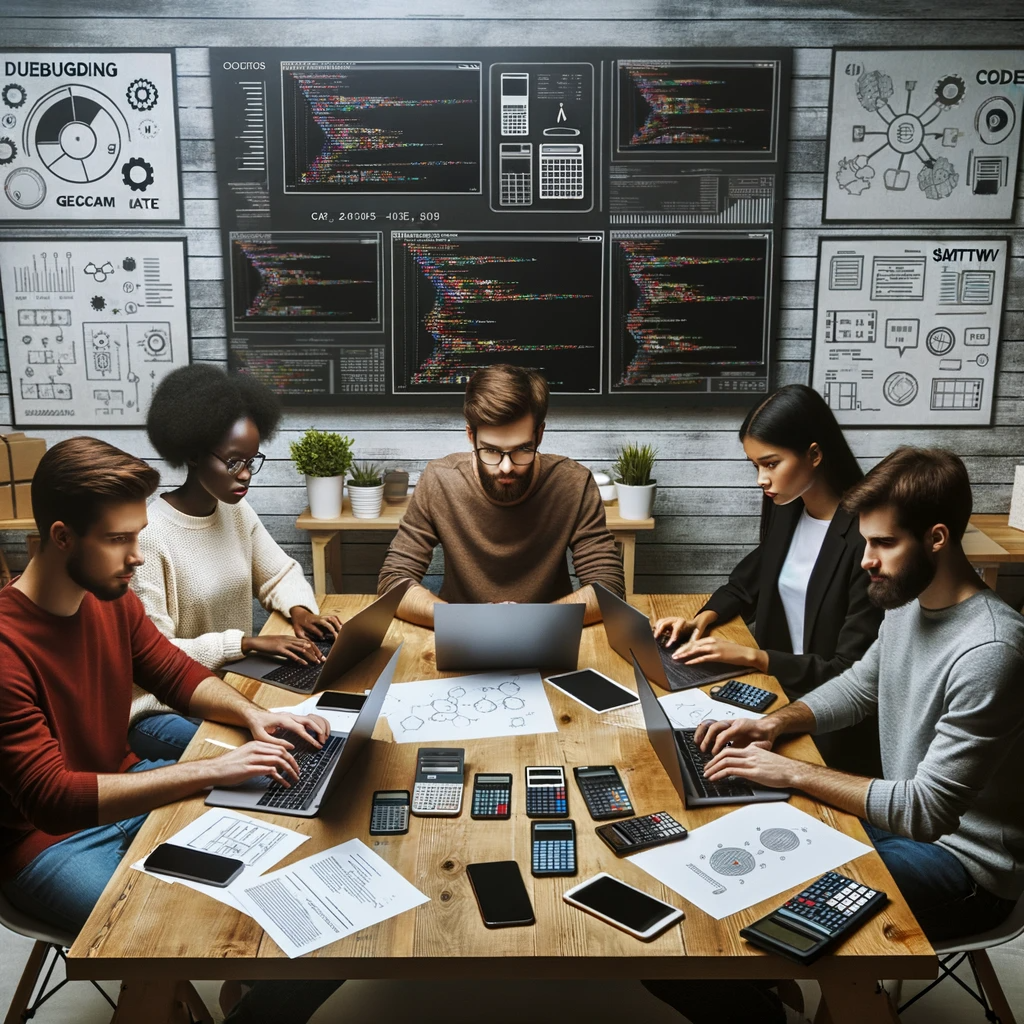
GEG Calculators is a comprehensive online platform that offers a wide range of calculators to cater to various needs. With over 300 calculators covering finance, health, science, mathematics, and more, GEG Calculators provides users with accurate and convenient tools for everyday calculations. The website’s user-friendly interface ensures easy navigation and accessibility, making it suitable for people from all walks of life. Whether it’s financial planning, health assessments, or educational purposes, GEG Calculators has a calculator to suit every requirement. With its reliable and up-to-date calculations, GEG Calculators has become a go-to resource for individuals, professionals, and students seeking quick and precise results for their calculations.