Aluminum Rivet Weight Calculator
FAQs
- How much weight can an aluminum rivet hold? The weight-bearing capacity of an aluminum rivet depends on various factors such as its size, material strength, and installation method. Different types of aluminum rivets can have different load capacities. It is crucial to choose the right type and size of rivet for a specific application to ensure proper performance.
- How much weight can a 1/8 rivet hold? The load capacity of a 1/8-inch rivet will depend on the specific type of rivet, the material it is used on, and the quality of installation. Generally, smaller rivets have lower load capacities compared to larger ones. For critical applications, engineering calculations or manufacturer specifications should be consulted to determine the exact load capacity.
- How do you calculate rivets? To calculate the required number of rivets for an application, you need to consider the joint design, material thickness, and the load it will carry. There is no single formula for this calculation, as it varies based on the specific application and the type of rivet being used. It is advisable to consult engineering handbooks, design manuals, or seek guidance from a professional engineer for precise calculations.
- What is the allowance for rivets? The allowance for rivets refers to the gap or space left between the sheets or components being joined by the rivets. This allowance is essential to accommodate the expansion and contraction of materials due to temperature variations and to ensure the rivet can properly grip the materials during installation.
- What is the strength of a 3/16 aluminum rivet? The strength of a 3/16-inch aluminum rivet will depend on its specific material grade and type. Different types of aluminum rivets have different strength ratings. For critical applications, it is best to refer to manufacturer specifications or engineering data to determine the exact strength.
- Are aluminium rivets strong? Yes, aluminum rivets are generally considered strong, especially when used in appropriate applications. They are lightweight, corrosion-resistant, and widely used in various industries, including aerospace, automotive, and construction.
- How strong are Aluminium pop rivets? Aluminum pop rivets are widely used for non-structural applications. Their strength varies based on the size, type, and material grade. For lightweight applications, they can be sufficiently strong, but for heavy-duty or structural purposes, other types of rivets might be more appropriate.
- How strong are rivets compared to screws? Rivets and screws have different load-bearing capacities based on their design and installation methods. In general, screws can have higher shear and tensile strength compared to rivets. However, rivets are preferred for certain applications due to their ability to distribute loads and prevent material pullout.
- How much should a rivet stick out? The amount a rivet should stick out (called “rivet tail” or “rivet upset”) depends on the type of rivet and its installation method. Generally, the rivet tail should protrude enough to form a secure and robust joint without causing any interference or safety issues.
- What is the formula for the bearing strength of a rivet? The formula for the bearing strength of a rivet involves calculating the load-bearing capacity of the rivet based on its diameter and the thickness of the material it’s passing through. The exact formula can vary depending on the type of rivet and the specific application. It is advisable to consult engineering references or standards for the precise formula.
- What is the normal spacing between rivets? The normal spacing between rivets (also known as “pitch”) depends on the joint design, material thickness, and the required load-carrying capacity. In general, rivets are spaced in a manner that provides sufficient strength while avoiding excessive deformation or distortion of the materials being joined.
- What is the minimum distance between rivets? The minimum distance between rivets is typically determined by design considerations, including the material thickness, rivet diameter, and load requirements. It is essential to follow industry standards and design guidelines to ensure the structural integrity of the joint.
- What is the rivet rule? The “rivet rule” may refer to different guidelines or best practices related to riveting. Without specific context, it is difficult to determine which rule is being referred to.
- Are rivets cheaper than bolts? In general, rivets can be more cost-effective than bolts, especially in high-volume production or automated assembly processes. Riveting requires less labor and tooling compared to bolting, making it a more economical option for certain applications.
- Are rivets cheaper than welding? Riveting can be more cost-effective than welding in certain scenarios, particularly when large quantities of joints need to be made quickly and efficiently. Welding can require more labor, skill, and equipment, which can increase the overall cost.
- Is rivet stronger than welding? The strength of a joint made by riveting or welding depends on various factors, including the materials, joint design, and load requirements. Both riveting and welding can create strong joints when done correctly, but the choice between the two methods depends on the specific application and design considerations.
- Can I use steel rivets on aluminum? Yes, steel rivets can be used on aluminum, but it’s essential to consider the potential for galvanic corrosion when using dissimilar metals. To avoid corrosion issues, you can use aluminum rivets or coat the steel rivets with a suitable protective coating.
- What rivets are strongest? The strength of rivets depends on the material, size, and type. In some applications, high-strength steel or structural-grade aluminum rivets may be used for increased load-bearing capacity.
- Is it better to weld or rivet aluminum? Whether to weld or rivet aluminum depends on the specific requirements of the application. Welding may provide a more continuous and seamless joint, while riveting can be quicker, easier, and more cost-effective for certain assembly processes.
- What is the difference between hard and soft aluminum rivets? Hard aluminum rivets are more durable and provide higher strength, but they require higher installation forces. Soft aluminum rivets are easier to install but offer lower strength. The choice between hard and soft aluminum rivets depends on the specific application and load requirements.
- Will aluminum rivets melt? Aluminum rivets have a melting point, like any other material. However, during the installation process, the rivets are not typically subjected to temperatures high enough to cause them to melt.
- Are stainless steel rivets stronger than aluminum? Stainless steel rivets are generally stronger than aluminum rivets due to the higher tensile strength of stainless steel compared to aluminum. However, the choice of rivet material depends on the specific application and requirements.
- Are pop rivets stronger than bolts? In general, bolts can have higher load-carrying capacities compared to pop rivets. Bolts offer more flexibility in terms of size, length, and material options, making them suitable for various heavy-duty applications.
- Do rivets loosen over time? Rivets can experience loosening over time, especially if they are subjected to constant vibrations or dynamic loads. Proper installation techniques and choosing the appropriate rivet type can help minimize the risk of loosening.
- What are the disadvantages of rivets? Some disadvantages of rivets include the need for access to both sides of the joint during installation, the potential for rivet heads protruding, and the possibility of rivets loosening over time in dynamic applications.
- Why are rivets no longer used for steel construction? Rivets were widely used in steel construction during the 19th and early 20th centuries. However, advances in welding technology and the availability of high-strength bolts led to the gradual shift away from rivets in steel construction. Welding and bolting provided more efficient and cost-effective methods of joining steel members.
- How thick of material can you use a rivet nut on? The thickness of material suitable for a rivet nut depends on its type, size, and material strength. Rivet nuts can be used on relatively thin materials, typically starting from around 0.020 inches (0.5 mm) up to several inches thick, depending on the specific rivet nut.
- What happens if you use too long of a rivet? Using a rivet that is too long for the material stack can lead to improper installation, deformation, or interference with adjacent components. The rivet’s length should be appropriate for the thickness of the materials being joined.
- How do you install solid aluminum rivets? Installing solid aluminum rivets typically involves placing the rivet in a pre-drilled hole and using a bucking bar and rivet gun to deform the tail of the rivet, securing the materials together.
- Does rivet length matter? Yes, rivet length matters as it should be suitable for the thickness of the materials being joined. A rivet that is too short may not form a secure joint, while a rivet that is too long can cause problems during installation.
- What is the strength of AN470 rivets? AN470 rivets are aircraft-grade rivets with specific material and performance specifications. Their strength can vary based on the size and material grade, so it’s best to refer to the manufacturer’s data for precise strength values.
- How do you calculate bearing weight? The bearing weight is calculated based on the bearing area of the joint and the allowable bearing stress of the materials being joined. The formula involves multiplying the bearing area by the allowable bearing stress to determine the maximum bearing load.
- How do you calculate fastener strength? Fastener strength depends on the type of fastener and the materials being joined. The calculation involves determining the axial load or the combination of axial and shear loads that the fastener can withstand before failure.
- What size hole do you drill for a rivet? The size of the hole drilled for a rivet should match the nominal diameter of the rivet. The hole size is typically slightly larger than the rivet’s shank diameter to allow for easy insertion during installation.
- What is the recommended hole size for rivets? The recommended hole size for rivets is usually specified by the rivet manufacturer or engineering standards. It should be large enough to accommodate the rivet’s shank and provide enough clearance for insertion.
- What is the maximum edge distance for rivets? The maximum edge distance for rivets depends on the specific rivet type and application. It is essential to follow industry standards and guidelines to ensure a safe and robust joint.
- What is the effective length of rivets? The effective length of a rivet is the portion of the rivet that is contributing to the joint’s strength. It is typically the shank length of the rivet, excluding the head and tail portions.
- What is the smallest allowable rivet diameter for rivet pitch? The smallest allowable rivet diameter for rivet pitch depends on the application and the materials being joined. It is essential to consider the load requirements and the joint’s design to determine the appropriate rivet diameter and pitch.
- What is the term for the distance between rivets in the same row? The term for the distance between rivets in the same row is called “rivet pitch.” It refers to the center-to-center spacing of rivets along a row.
- Which side of a rivet to hammer? When installing a rivet, the hammering or deformation is usually done on the opposite side of the head. For example, if the head of the rivet is on the top side of the joint, the hammering is done on the bottom side.
- What happens if rivet is too short? Using a rivet that is too short for the material thickness can result in an insecure joint with reduced load-carrying capacity. The rivet may not properly expand or deform to securely hold the materials together.
- What is the difference between a blind rivet and a normal rivet? A blind rivet, also known as a pop rivet, is designed to be installed from one side of the joint, requiring access only from one side. In contrast, a normal rivet requires access to both sides of the joint during installation.
- Why use screws over rivets? Screws offer more adjustability and can be removed and reinstalled, making them more suitable for applications where disassembly may be required. Rivets are often preferred for permanent, tamper-resistant joints.
- Why are rivets obsolete? Rivets are not considered obsolete; they are still used in various industries and applications. However, advances in welding and bolting technology have made these methods more convenient and practical for certain applications.
- Why are rivets not used? Rivets are still used in many applications due to their advantages, but they may not be used in certain scenarios where welding or bolting provides better performance or cost-effectiveness.
- Why are planes riveted and not welded? Aircraft are often riveted instead of welded for several reasons. Rivets provide flexibility, easier repairs, and the ability to join dissimilar materials without causing localized distortion. Rivets also distribute loads more effectively than welds, which is essential in aircraft structures.
- Are steel or aluminum rivets better? The choice between steel and aluminum rivets depends on the specific application, material compatibility, and load requirements. Both types of rivets can be strong and effective, but each has its advantages and limitations.
- What metal is best for rivets? The best metal for rivets depends on the specific application, environmental conditions, and load requirements. Common materials for rivets include aluminum, steel, and stainless steel.
- What is the best alternative for rivets? The best alternative for rivets depends on the specific requirements of the application. Bolts, screws, welds, or adhesive bonding can serve as alternatives, each with its own advantages and limitations.
- Are rivets as strong as screws? The strength of rivets and screws depends on the specific application and materials being joined. In certain situations, screws may have higher strength, while rivets are preferred for their ability to distribute loads more evenly.
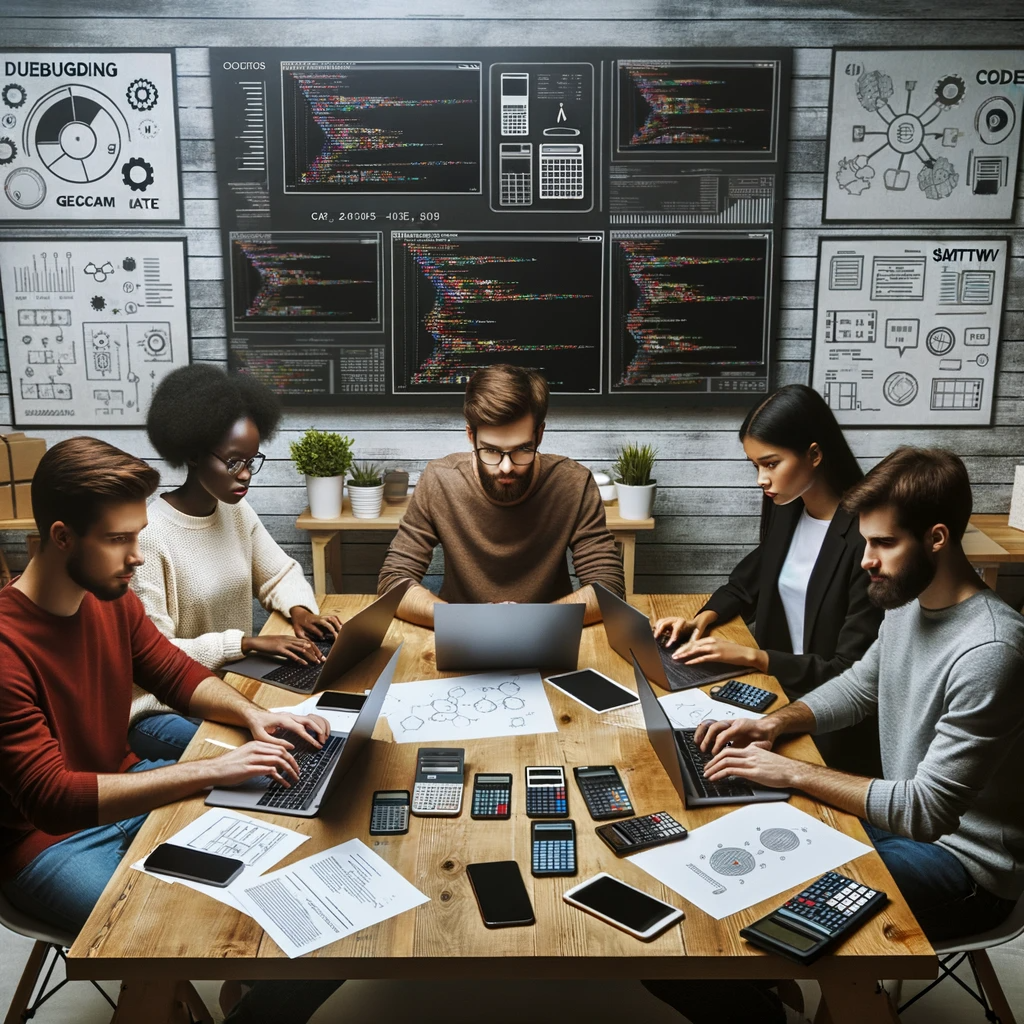
GEG Calculators is a comprehensive online platform that offers a wide range of calculators to cater to various needs. With over 300 calculators covering finance, health, science, mathematics, and more, GEG Calculators provides users with accurate and convenient tools for everyday calculations. The website’s user-friendly interface ensures easy navigation and accessibility, making it suitable for people from all walks of life. Whether it’s financial planning, health assessments, or educational purposes, GEG Calculators has a calculator to suit every requirement. With its reliable and up-to-date calculations, GEG Calculators has become a go-to resource for individuals, professionals, and students seeking quick and precise results for their calculations.